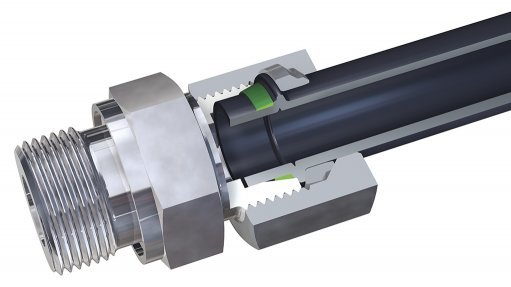
Eaton's Walterscheid WALFORMplus-SR system
A truck-mounted loader crane manufacturer is said to have significantly lowered its fuel consumption thanks to a reduction in tube weight, while also eliminating tube failures.
Eaton asserts that by switching to its Walterscheid tube-fitting and forming technology, the manufacturer, which is a specialist in class-leading load-handling equipment, has made simultaneous improvements in the areas of weight and strength.
The company explains that the primary objective was to reduce weight across the loader crane, as less weight means less load and less fuel consumption for users, while also preventing tubes from cracking or bursting, a potential problem that is exacerbated by the side-load function of the loader crane imparting high mechanical stress on the tubing.
To achieve this objective, higher strength E355 grade tubing with thinner wall thickness was used to replace standard E235 tubing on the loader cranes. E355 seamless cold-drawn tubing is said to offer higher tensile strength than standard tubing, at a lower net weight. The elevated strength of E355 allows users to achieve similar operating pressure for thinner tubing, and the manufacturer was able to switch from 16-mm-diameter, 2-mm-thick E235 tubing, to 16-mm-diameter, 1.5-mm-thick E355 tubing. The 0.5 mm difference in wall thickness reduced the weight from 0.69 kg/m to 0.54 kg/m, achieving a 22% saving.
Eaton’s Walterscheid WALFORMplus-SR system is said to extend the advantages of the WALFORM platform to thin-wall tubing such as the 16 mm x 1.5 mm product identified for the application. An additional support ring (SR) located behind the formed tube is used to increase resistance to vibration and bending stress.
The system is a positive-locking, cold-forming tube-fitting system designed for increased safety, even under extreme loads. The mechanically reshaped tube-end screws together using an additional support ring, as well as a conventional DIN/lSO stud and a DIN/lSO union nut. In addition, any possible leakage path is sealed-off by the WALFORMplus soft seal and the metal-to-metal seal between the patented WALFORMplus shoulder and the fitting stud. The positive-locking connection and additional support ring helps to ensure secure retention and greater resistance to dynamic loads.
The company details how simulated pressure impulse and bending stress tests in its laboratory demonstrated that the system could offer a higher resistance against dynamic load compared with other forming systems, resulting in longer operating life and this was further attested to in the actual application. The geometry of the reshaped tube is designed to ensure optimum performance under dynamic loads such as reversed bending stress and dynamic pressure impulses.
The adoption of WALFORMplus-SR and thin-walled E355 tubing material helped the manufacturer to optimise both the strength and weight of its mobile loader cranes, with the latter contributing to reduced fuel consumption.
Among further advantages, the manufacturer now enjoys the protection of Walterscheid Guardian Seal plating, which is particularly important in environmentally challenging applications such as mobile loader cranes. Their location on the rear of a truck exposes these lifting devices to the elements, as well as salt spray and other contaminants from the road surface. Guardian Seal is a zinc-based surface treatment applied by electroplating. The 11-µm- to 15-µm-thick zinc ensures high levels of protection against corrosion and meets DIN EN ISO 9227 standards.
Another benefit is simplified assembly, as a result of short tightening rotation and low torque.
Eaton says that the WALFORM machines located on the manufacturer’s production lines across Europe are delivering repeatable steel tube assemblies for the company and its customers. To automate the process Eaton manufactures its own assembly machines to optimise the production of Walterscheid systems.
For WALFORM 6 mm to 42 mm in diameter, the company offers the M-WF385Xplus, for demanding tube-forming applications in steel and stainless steel, enabling additional sealing, easy machine assembly and robust performance. Fast cycle times allow for efficient and economical production, while simple and quick tool changes reduce set-up times. In addition, tools are colour-coded to ensure accuracy in the forming process.