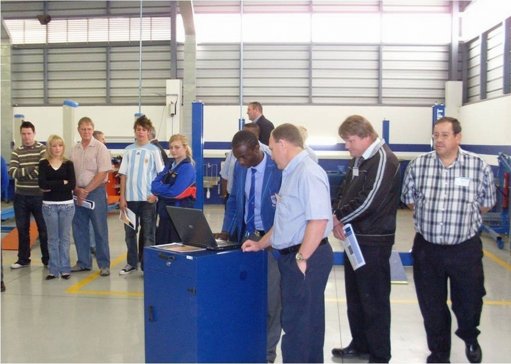
COMPUTER DIAGNOSIS Learners are exposed to real-time aspects of the motoring sector, like technology advances in components and diagnostics
Car manufacturer Hyundai Automotive South Africa (HASA) launched the Hyundai Training Academy, in Bedfordview, Johannesburg, in November, to address the serious shortage of available skills in South Africa’s within the automotive industry.
The Hyundai Training Academy is an academy dedicated to product training (technicians, service advisers and sales persons) and development training (apprentices and school projects), says HASA national service manager Henry Gerber.
Besides the challenge of training and accommodating staff, Gerber says getting people interested in the automotive industry is the biggest challenge.
HASA after-sales GM Michael Prigmore says that many people still associate working in the automotive industry with tasks assigned to mechanics.
However, Hyundai has been creating awareness among learners in high schools to expose students to the modern technology used in the automotive industry, he says.
HASA service director Michael Rohde explains that “training is offered to each school as part of its normal daily class schedule; however, more complex motor issues pertaining to motoring are discussed”.
Further, learners are exposed to the real-time aspects of the motoring sector, like technology advances in components and diagnostics. In this way, a detailed understanding is fostered, he adds.
The school has a curriculum set by the Department of Education. As a service, HASA will offer additional information and training on subject matter relating to the technological basis of requests from schools.
The Hyundai Apprentice Programme is not aimed at enriching the brand, but rather to focus on the entire motor indus-try, says Gerber. He estimates that there is a shortage of 40 000 skilled employees in the automotive industry.
The future plan of the academy, says Gerber, is to reduce the average age of technicians from the mid-40s to the mid-30s, adding that if more people are qualified, there will be a younger pool from which to draw expertise, reflecting the vitality of the industry, part- iculary in terms of artisans.
Further, the company aims to employ one apprentice for every technician, as this type of per- sonal training can guarantee sustainability, he says, adding that there is currently a ratio of 0.8:1, which denotes a 20% fill requirement.
Currently, there are 113 apprentices at the academy, 15% of whom are rotated every six months. The duration of the apprenticeship is two-and-a-half to three years, after which an apprentice qualifies as a technician. The newly qualified technicians can either remain with Hyundai or move on to other companies.
However, constant training is necessary, as five years without training will result in an artisan becoming redundant in terms of technological advances, says Gerber. Although a matric qualification is a requirement, with maths and science being a minimum requirement, the company does make exceptions in South Africa.
“While we promote the achievement of a Grade 12 qualification and, where possible, a tertiary degree or diploma, it is a reality that not all learners have the ability or socioeconomic opportunity to achieve this. “Thus, we use this programme as a platform for equality, enab- ling these youths to become qualified in a field of expertise of their choice that would normally not have been available to them,” says Rohde.