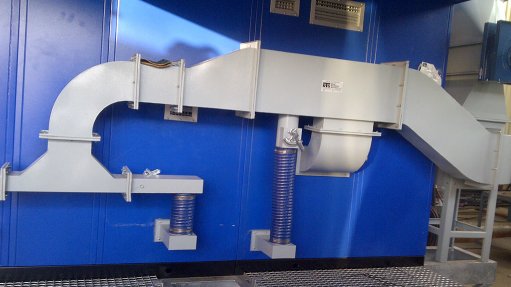
LASTING INSTALLATION Rand Technical Services supplied dedicated back channel cooling to variable speed drive (VSD) panels in a control room on a mine in the Northern Cape
A key benefit of Tshwane-based specialised engineering solutions company Rand Technical Services’ (RTS’) spin filter technology remains its maintenance-free features, which provide a compelling motivation for companies to use this technology, RTS MD Ian Fraser notes.
Costly maintenance in numerous applications from mining to manufacturing is virtually completely avoided once spin filter technology is installed, Fraser tells Engineering News, pointing out that conventional filtration methods often require continuous maintenance and filter-membrane replacement.
“RTS has installations that are still in good condition after 23 years,” Fraser says, noting that this technology is widely applied in mining environments with heavy dust loads, including at control and transformer rooms, substations, machinery spaces and workshops, as well as at power stations and steel mills.
Companies in these sectors face growing pressures of containing costs and maintaining profits while overcoming industry challenges, he points out.
As a result, companies are looking towards the engineering industry to offer ways of reducing costs and downtime through innovative technologies, improved industrial processes and cost-saving efficiencies.
In light of this, Fraser emphasises the efficiency of the spin filters, which also provide a rapid return on investment, owing to lower filtration maintenance and replacement costs, as well as a continuous reduction in equipment breakdown and support costs.
“All inertial spin filter installations are effectively motivated by a need to reduce maintenance and downtime,” he says, noting that RTS provided the technology for mining major Anglo American Platinum’s Mogalakwena platinum mine, in the North West.
RTS designed an air-filtering unit that could run at 32 000 Nm3/h, which was installed in January.
In addition, mining and petrochemicals design and project management services consulting firm ProProcess has specified that RTS spin filters be used at two of its mining projects – one in the Northern Cape and one in the Democratic Republic of Congo.
A spin filter unit is a high-efficiency application of robust and simple cyclone technology, with almost no moving parts and, therefore, little wear and tear.
In addition, unlike conventional filter membranes that clog because of pressure build-up after a period of use, the pressure drop across the spin filter module never increases. This results in self-cleaning units that do not clog when correctly installed, thereby offering consistent performance with constant resistance, Fraser highlights.
He adds that, as no secondary filtration is required for the application of RTS inertial spin filters to clean the air, the need for expensive, complex and high-maintenance bag houses has been eliminated.
Other products that provide enhanced efficiency and maintenance reduction costs include the Neo Monitors laser gas monitors, which were first launched in 2009.
Gas analysis has historically been conducted through probes, which can be problematic, as gas streams tend to be dirty, hot and inaccessible, Fraser points out.
“Moreover, normal probes clog up easily, are affected by high temperatures
(subsequently affecting the accuracy of the readings) and can also have a short life span, thereby requiring extensive maintenance,” Fraser says, highlighting that tunable diode laser technology offers a viable alternative to probe-based instruments.
The laser monitor is not negatively affected by high temperatures and is tuned to a specific, specially selected absorption line for a particular gas, which enables the instrument to measure the level of the selected gas in the gas stream without cross-interference from other gases or contamination by dust particles.
“These monitors are accurate, durable and, therefore, a cost-effective means of measuring and analysing a large range of gases,” Fraser says, concluding that maintenance consists of only a simple yearly calibration check.