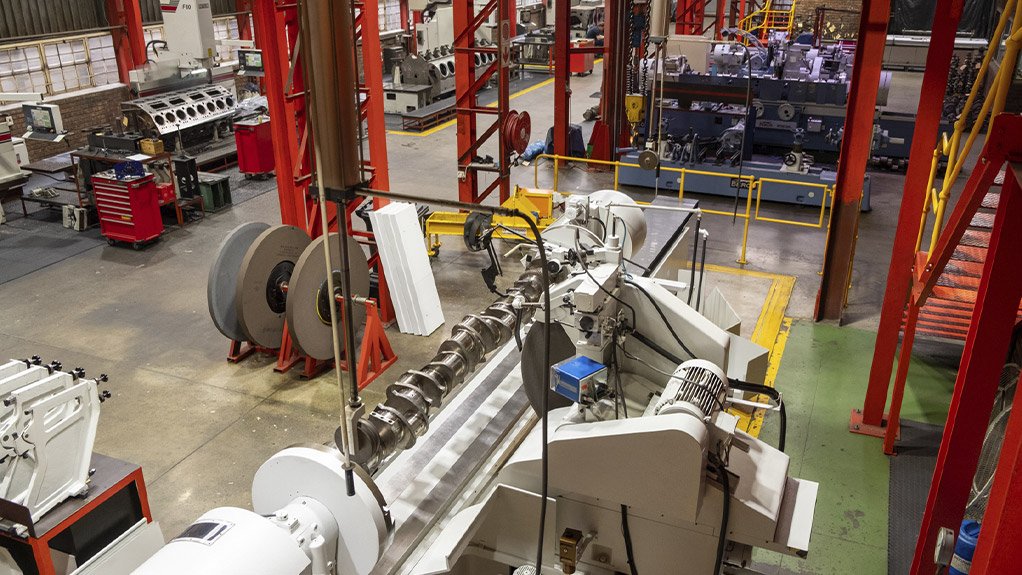
Investing in its people has for decades been the foundation of Metric Automotive Engineering's success
Technical excellence in large diesel and gas engine component remanufacturing relies as much on top-class artisan expertise as it does on advanced and specialised equipment, says Andrew Yorke, operations director at Metric Automotive Engineering.
“This is why our ongoing investment in our people and their skills creates the real asset underpinning our technical capability,” says Yorke. “In the same way that we re-invest in our world class equipment, we are constantly upgrading our skill sets and empowering new employees.”
He highlights the vital role in South Africa’s economy for structured and closely supervised learning of trades, which Metric Automotive Engineering has been systematically conducting for decades. From the previous apprenticeship system to the current learnership programmes, the company’s technical staff have grown into demanding senior positions. They also then assume responsibility for passing on their knowledge to new learners.
“We work closely with the Manufacturing, Engineering and Related Services Sector Education and Training Authority (Merseta) to achieve the required competency-based outcomes,” he says. “At the same time, our learning process aligns with our ISO accreditation to ensure that the expertise we generate is globally competitive.”
The training of new entrants through to journeyman status – or artisans – has been central to Metric Automotive Engineering’s business model since day one. The meticulous sharing of experience and skills from the company’s ‘custodians of knowledge’ has allowed a steady supply of committed experts to gain the best value from its leading-edge machinery.
“Customers have always been able to rely on the quality of our workmanship, as the depth of our skills base allows us to apply all the necessary ISO checks for optimal results,” he says. “This is also the basis of our culture of quality, where each person on our workshop floor feels the pride of being part of a smoothly functioning environment.”
The learning process ensures that a wide range of skills is covered, giving each learner a rounded capability and an integrated understanding of the workshop equipment and processes. This contrasts with an approach that leaves staff overly focused on a limited number of tasks – restricting their growth and abilities.
“Our multi-skilled approach rather gives our artisans greater variety and fulfilment in their work and career development,” says Yorke. “It also gives our workshop greater capacity to absorb high work-flows while still ensuring that customers receive high quality results.”
He notes the importance of technical trades like automotive machining in opening up career opportunities for young South Africans. School-leavers with science and mathematics at matriculation level can enter exciting careers through structured learnerships. Such programmes can provide skills of life-long value, as artisan expertise evolves over time to meet new equipment demands and sophistication.