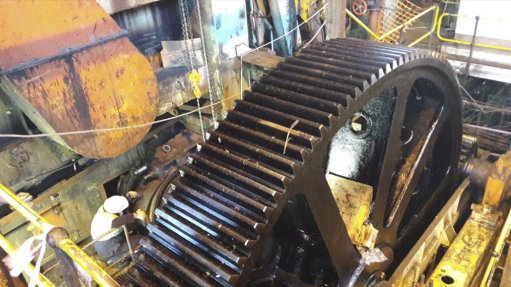
OPERATION EFFICIENCY BMG's services assist in enuring sugar processing plants are prepared for high productivity season
Engineering solutions provider BMG’s Regional Service Centre (RSC) in Riverhorse Valley, KwaZulu-Natal, plays a critical role in the sugar sector by providing engineering solutions designed to optimise productivity for sugar growers and millers.
“Our dedicated service centre, which focuses on core KwaZulu-Natal divisions – including hydraulics and pneumatics, drives, bearings, gaskets and materials handling – operates closely with 11 dedicated BMG KwaZulu-Natal branches, to meet every customer’s specific requirements,” says BMG KwaZulu-Natal RSC manager Keith van Wyk.
“BMG’s specialist service centre, with assembly, repair, maintenance and support operations, offers a combined technical expertise and value-added product solutions. Benefits for customers include a dependable service, repair and delivery efficiencies, centralised technical support and easy accessibility to BMG’s comprehensive range of quality branded engineering components.
“An important area of growth for BMG is in the sugar industry. “The KwaZulu-Natal field service team has been involved in a number of field service projects locally and in neighbouring States, during recent off-crop seasons, as well as dealing with urgent breakdowns in sugar mills and refineries.”
The RSC’s specialist services include bearing and gearbox inspection, bearing and chain refurbishment, large size bearing assembly and alignment and balancing, as well as customised product design.
The BMG team has recently completed a refurbishment, fabrication and replacement project to refurbish and replace worn components in preparation for high productivity in the upcoming season.
Dorstener gearboxes have been used on diffuser drives, mill drives and feeder tables for many years and three of these planet carriers recently needed to be replaced, due to excessive bearing journal wear and cracking.
“In spite of tight time restrictions before the seasonal startup of the mill, coupled with manufacturing challenges, BMG has designed, fabricated and installed new carriers, reducing the normal 24-week delivery period to only four weeks, with cost savings of about seven-and-a-half times that of the original-equipment manufacturers,” explains BMG engineering GM Mike Cooper.
“Carriers are normally manufactured by Dorstener from cast iron, which is extremely difficult to repair. “In this case, there was the additional problem of bores positioned close together, with virtually no wall thickness between the bearing journals, which was where the cracking had occurred. Because of the harsh operating conditions of the mill and the high torque load of these units, we decided replacement was the preferred option over refurbishment.”
He adds that these planet carriers were re-engineered and fabricated out of 355WA steel plate, which is not only stronger than the original cast iron units, but also allowed BMG to manufacture these carriers in a far shorter lead time of three weeks.
The team was on a tight deadline to have drawings and designs approved to ensure highly accurate dimensions for a perfect fit with clearances to accommodate the gear mesh.
Welding challenges to maintain the structural rigidity of the system were overcome by machining interlocking tabs in the top and bottom main plates, as well as in the webs and side rings, to ensure a more precise assembly for welding, with less distortion.
The webs and side plates were welded to the bottom ring and the entire assembly was then fitted onto the top ring, for welding into place. Slots were later filled with weld, so that the webs formed an integral part of the structure.
BMG’s total plant maintenance solutions are geared to optimise productivity and enhance process plant operating reliability to make a difference to the efficiencies of the sugar sector.