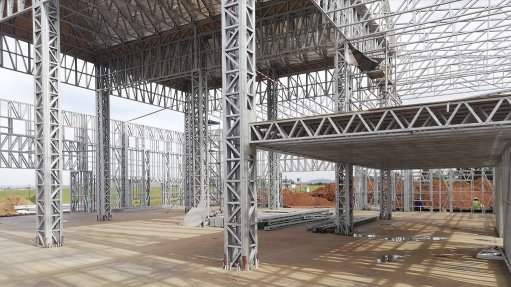
MARKET GROWTH The sub-Saharan Africa market for LSFB has grown as much as the South African market, and it continues to grow
The Southern African Light Steel Frame Building Association (Sasfa) aims for light steel frame building (LSFB) to be used for at least 10% of all new building projects in South Africa.
When achieved, it will create a sustainable market of at least 32 000 t/y of high-strength galvanised steel sheet. Sasfa currently has 62 member companies and it aims to expand the LSFB market to members’ benefit.
The sub-Saharan Africa market for LSFB has grown as much as the South African market, and it continues to grow. This means that the LSFB market potential can be doubled, says Sasfa director John Barnard.
As a division of nonprofit organisation the Southern African Institute of Steel Construction, Sasfa’s activities involve the promotion of all the major materials used in this sector.
“Steel constitutes 60% of the value of materials involved in LSFB, while gypsum board, insulation and fibre cement board, as well as FC planks, comprise the other 40%. “Specialist external insulation cladding systems are also used in a growing number of projects,” he says.
Barnard states that the LSFB market has grown from zero to about 300 000 m2/y. The association believes that this market would not have existed had it not been for Sasfa and its continued efforts to promote the LSFB market.
“Our international ‘sister’ organisations have expressed surprise at the rapid rate at which LSFB has developed in South Africa – especially in view of our history of masonry building. The fact that Sasfa members can be regarded as reputable suppliers is pleasing.
“If we receive a complaint about a member company, it is investigated immediately, and corrective measures are agreed to with the member, if applicable. If the member does not comply with such measures within the agreed time, its membership is suspended,” he asserts.
Sasfa has maintained a close working relationship with the built environment division of the Council for Scientific and Industrial Research. This contributed to LSFB being accepted as a viable alternative building method by the Presidential Infrastructure Coordinating Commission.
The commission decided to encourage the use of alternative building methods for hospitals, schools, clinics and other public buildings such as government offices.
“LSFB was used for the offices of the Department of Health, in KwaZulu-Natal, which was built within 11 months. This is testimony to the speed of construction, which is possible with LSFB, as well as the thermal and acoustic properties of the insulated walls. The success of this project is bound to lead to further government projects in the future,” Barnard suggests.
Further, he points out that there is a new trend in South Africa to use LSFB to premanufacture pods such as hotel rooms. Manufacturing takes place in a factory under controlled conditions, with the pods delivered fully assembled to site. The first hotel of this nature is being “assembled” in Gauteng.
As Sasfa’s purpose was to establish and develop the LSFB sector in Southern Africa, the association compiled a building code and assisted the South African Bureau of Standards in turning it into the SANS 517 for LSFB.
“We also established training courses which are regularly presented and have been promoting the benefits of LSFB by exhibiting at trade shows and through lectures to interest groups and students.”
Sasfa also publishes articles on LSFB projects in the media, while an accreditation scheme for the different facets of LSFB has been drafted to help ensure quality in the sector, he concludes.