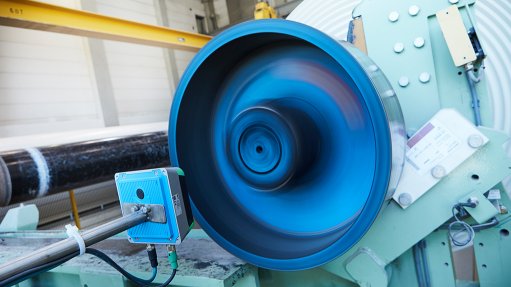
To maintain an overview of its multistep production process, German paper mill Kabel Premium Pulp & Paper uses a radio-frequency identification (RFID)-based solution, integrated in a high- performance, wireless transmission system with an interface as part of its own in-house information technology (IT) system.
“This enables workers at Kabel to constantly track which production step is currently being processed by a given paper batch,” says Roodepoort-based intelligent sensor solutions supplier SICK Automation.
Two giant paper machines and 540 workers operating in a three-shift rotation handle a total capacity of around 485 000 t/y at Kabel’s Hagen-based facility.
Depending on the particular paper thickness, the rolls, or tambours, measuring 7.2 m wide, carry about 50 000 m to 60 000 m of product and weigh up to 20 t. The paper is wound onto metal cores so that the rolls weighing several tons can be transported.
These tambour cores are hung at their ends at each stage of production and are transported by the overhead cranes. About one hundred of these tambour cores are in continual use at the Hagen factory.
Therefore, production faults can mean tens of thousands of metres of wasted paper. To reliably monitor the production of each individual roll, Kabel Premium Pulp & Paper uses a custom- made RFID solution from system integrator Intelligent Data Service (IDS), with 26 RFID reading devices provided by the sensor experts at SICK.
“We required a solution to ensure the automatic detection of tambour cores in the production flow,” explains Johannes Broer, who is responsible for IT at Kabel Premium Pulp & Paper.
“Our requirements included, among other things, reliable system components and wireless data transmission to our IT system. The components used are exposed to process-related contamination, dust and heat. They must be able to withstand contact with chemicals or machine oil. We had to rule out optical detection-based solutions, owing to the risk of contamination. This was also the case for visual markings, which do not stand up to contact with oil, for example.”
In addition, a solution with very short read times was required, since the tambours are constantly in motion. “We mark our tambours with an eight-digit number, which comprises both the date of production as well as the year. The tambour cores feature a three-digit number. Apart from the fact that the reading stations can be hard for our workers to reach, the long numbers can also result in manual input errors. Automated detection allows us to ensure accurate tracking and relieve some of the burden on our workers,” says Broer.
This is why the tambour cores are marked with passive RFID tags, which are read at individual stations.
However, to optimally align systems to the individual application, the application specialists from SICK carefully inspect the situation on-site at the factory. A number of aspects had to be observed in this case as metal reflects radio waves and can result in system faults. It is for this reason that the RFID tags on the metal cores had to be strong to a point that close proximity to metal would not pose a danger.
IDS integrated the SICK reading devices into its roll online tracking system, known as “Rolf”, which it had developed itself.
The system collects all results directly from the RFID reading devices, visualises them, and makes the data available for further processing.
Contact: Rema Hattingh (Cubic Ice)
Company: SICK Automation
Tel: +27 (0)11 705 2545
Email: remah@CUBICICE.COM