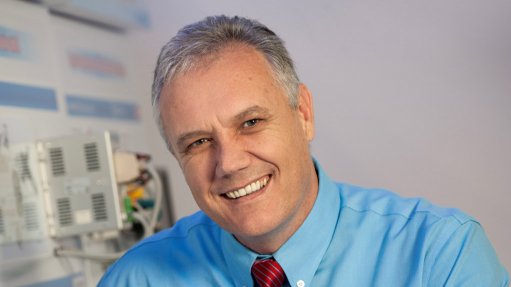
ERNST SMITH The regulated compressed-air in pneumatics is clean and therefore perfect for the food and beverage industry
Pneumatic valve manifolds have the potential to be the safest means of mechanical driving for the food and beverage industry, as they use clean air to elicit movement in the manufacturing process, thereby eliminating food contamination risks.
There are many unique features of pneumatics as a solution in the food and beverage industry. For instance, pneumatics is hygienic and high in speed. Regulated compressed air is clean and therefore perfect for the food and beverage industry.
Hydraulics uses oil to stimulate an actuator. In such applications, oil leakages can lead to the contamination of foodstuffs whereas any leakages in pneumatic actuators will cause no contamination. Obstruction of movement of actuators will simply cause the process to pause instead of physical breakages, “all thanks to the marvels of compressed air”, says SMC Pneumatics product manager Ernst Smith.
Owing to these qualities and local assembly of the SY series in South Africa, there is an increase this year in demand for SMC’s latest SY valve manifold series for the food and beverage industry, he adds.
Pneumatic valve manifolds are especially beneficial to the food and beverage industry, which requires the use of valve manifolds with an ingress protection (IP) rating of 65, meaning that it has to be splash and dust proof.
“SMC’s SY5000 valve manifold specifically designed for the food industry is rated IP67, which means that it can be submerged up to 1 m deep in water for a brief period of time without affecting its operation. The design of this manifold’s housing makes cleaning and wash down more effective, compared with a standard industrial IP65-rated valve manifold,” says Smith.
The SY valve manifold series has been available on the international market for some time but has only in recent years been supported by SMC themselves on local shores. This manifold series comprises three valve sizes, namely the SY3000, SY5000 and SY7000. Based on different flow rates required, the customer is able to select the best suited valve for the application; this is easily configurable through SMC’s online SY configurator. Compared with earlier models, these valves offer higher flow rates for improved system performance or allow customers to downsize their valve size while reducing cost, he notes.
The SY series of valves have an impressive switching frequency of up to 20 Hz, enabling machine builders to easily automate demanding machine tasks such as capping, labelling, sorting and counting, explains Smith.
Compressed air is supplied to the manifold where valves direct air to where it is needed on the machine. Through one connection, either fieldbus or hard-wired multicore cable, manifolds are connected to a higher level controller responsible for the correct operation of the machine.
A unique feature of the SY manifold series is that the valves are available in either rubber-seal or metal-seal versions. The latter option is optimised for higher operating frequencies and extended lifetime performance, and facilitates guaranteed switching cycles in excess of 200-million. These valves incorporate an energy efficient V100 pilot valve with a power-saving option that reduces consumption (per valve coil) down to just 0.1 W.
Smith states that SMC South Africa plans on expanding into the rest of Africa in due course since it only opened its doors in Johannesburg last year, it has to focus its efforts on South Africa for now.