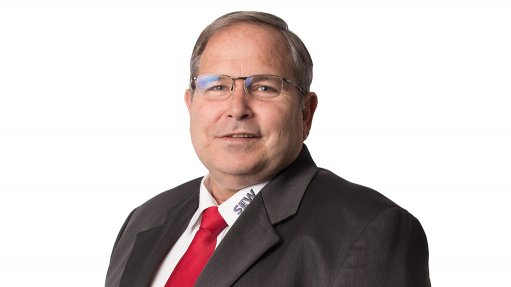
By Raymond Obermeyer, Managing Director, SEW Eurodrive
By Raymond Obermeyer, Managing Director, SEW Eurodrive
Many South African – and even African – companies don’t prioritise planned maintenance on their machinery and equipment to the same extent that companies in more developed countries do. This tendency to ignore regular maintenance has been exacerbated in the past year by the Covid-19 pandemic with many organisations running machinery until it literally breaks down.
There is no question that there is a cost associated with regular maintenance – but this cost is typically far lower than the cost of an unplanned breakdown which can have a catastrophic impact on production schedules and the sustainability of a business.
Planned maintenance involves regularly performing inspections, undertaking minor repairs and cleaning machinery rather than waiting for it to break down before any repairs are made. The benefit of planned maintenance is that potential problems and failures can be predicted and identified long before they become an issue. Replacement parts can be ordered in advance and budgeted for. It’s a preventative rather than a reactive approach which can provide significant savings both in terms of time and money.
Not only does following a recommended maintenance schedule reduce the likelihood of unexpected breakdowns and reduce unplanned downtime, but it also has the advantage of extending the life of machinery and equipment.
Those organisations that have availed themselves of SEW-Eurodrive’s service and maintenance contract typically benefit from more efficient operations, making their businesses more sustainable. They are able to plan shut down’s in order to replace equipment such as a gear box, for example. A significant part of our focus is on energy efficiency and safety technology. Wherever required, functional safety features are built into our equipment. We assist companies with regular maintenance and then compile a report where we recommend which parts will need to be replaced.
We recently assisted a beverage manufacturer to implement MOVIGEAR ® technology which is providing the company with a significant savings in terms of their energy costs. In fact, over the period of a year the cost of the new unit will be completely offset by the energy savings.
As a service provider to large-scale operations, the ability to respond quickly to breakdowns and provide solutions is critically important. SEW’s Field Service Department – which operates 24/7 - was recently approached by a platinum mining customer after hours about a failed gear unit. Within hours of the call a new gear unit solution had been built for the client and was installed and operating successfully. Commissioning to installation was completed in the same day. Having expected a much longer downtime, the client was delighted with the rapid response and the successful solution.
Key to our ability to respond quickly is a large local stockholding of leading technologies and solutions combined with highly skilled technicians who are able to service and repair products in the field.
Ends
SEW-Eurodrive is a specialist in drive and control technologies. It offers a comprehensive range of services to industry for the entire value chain including engineering and selection to start-up and maintenance. The company’s high quality complete drive solution for girth gears includes drive pinions, motors, coupling and support infrastructure while its segmented girth gears offer a flexible solution for diverse combinations. SEW-Eurodrive’s Field Service Department provides maintenance and condition monitoring services to customers. Available 24X7, 365 days a year, its support service team is able to carry out preventative maintenance or supply replacement units at short notice in order to reduce plant downtime.