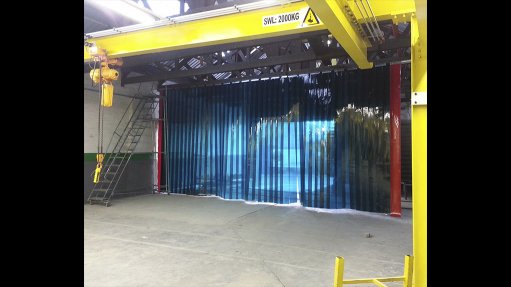
Zero tolerance is being exercised by the Department of Labour towards companies that do not comply with the health and safety regulations stipulated in the Occupational Health and Safety (OHS) Act. Wim Dessing, sales executive of Apex Strip Curtains & Doors, says this is particularly with regard to environments which are potentially hazardous to worker health.
OHS Compliance Easy With Apex Welding And Safety Screens
Zero tolerance is being exercised by the Department of Labour towards companies that do not comply with the health and safety regulations stipulated in the Occupational Health and Safety (OHS) Act. Wim Dessing, sales executive of Apex Strip Curtains & Doors, says this is particularly with regard to environments which are potentially hazardous to worker health.
“Welding and grinding are among the most notorious culprits for causing nasty accidents. This is not only in the immediate environment, but in the broader workplace through spreading noxious fumes and endangering the eyesight of those in the immediate vicinity,” he explains.
Dessing says it is not always feasible to provide solid wall barriers to counter UV radiation and weld splatter, due to cost as well as practicality, particularly in confined spaces.
“Some manufacturers resort to makeshift protective structures, erecting wooden or metallic partitions or even hanging opaque canvas sheeting from the ceiling and crossbeams,” Dessing continues. “None of these measures comply with the OHS Act and all fall far short of total worker protection and safety.”
The answer lies in installing Apex Welding and Safety Screens which not only protect workers from weld splatter and fumes, but also from harmful UV radiation.
Manufactured from a specially formulated PVC material which extensive SABS tests have proved to be far superior to conventional materials, the Apex Welding and Safety Screens come in various configurations to suit a variety of individual requirements. “The most popular version has a freestanding frame, allowing easy handling and portability,” Dessing says.
One of the most important design characteristics of the Apex Welding and Safety Screen is the patented Balledge® design on individual strips, which facilitates easy access for both personnel and equipment to cordoned-off areas.
“The feet of the screen are also angled to allow optimum utilisation of floor space,” Dessing adds. “And the screens can be butted together at a 900 angle.”
These features further promote ease of erection, making it simple to set up and arrange the screens in different shapes according to the specific demands of each particular workshop.
The screens absorb, scatter and filter the light spectrum to create a safer working environment for both the welder and any co-workers and supervisors in the immediate vicinity. Tested by the SABS for ultra-violet transmittance, conventional materials gave readings of 0.0005%, 0.008% and 5.0% as opposed to Apex readings of 0.005%, 0.001% and 0.005%. Tests for total visible light transmittance demonstrated incontestably that conventional materials permit 78% while Apex material allowed only 15.5% light transmittance – a dramatic difference, particularly when one considers long term exposure of workers and the consequent repercussions on their eyesight and even their skin.
“The Apex Welding and Safety Screens have the added advantage of being impervious to burning,” Dessing says. “This is important because materials can easily come into contact with welding splatter.”
Dessing cautions, however, that the welding screens are not intended as a substitute for proper eye protection nor to permit direct viewing of welding arcs at close range.