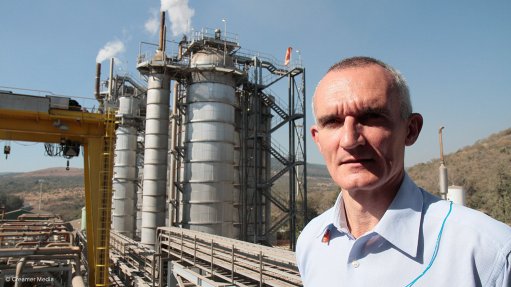
Sappi Southern Africa CEO Alex Thiel
Photo by: Duane Daws
The newly constructed Fibre Line 3 specialised cellulose plant at pulp and paper manufacturer Sappi’s Ngodwana mill, would ramp up to full capacity of 200 000 t/y by the end of this calendar year, Sappi Southern Africa CEO Alex Thiel told Engineering News Online on Wednesday following the official opening of the plant.
The Ngodwana mill had undergone a R3.3-billion modification, under the name of project GoCell, to enable it to produce specialised cellulose, in line with Sappi’s strategy of facilitating growth in specialised cellulose and other high-margin products.
Construction on the plant started in early 2012 with the first material produced mid-2013.
“[The launch is] not merely about celebrating the successful completion of a modernisation project. It is about seeing Sappi’s strategy for future growth and profitability in action,” Thiel said.
He added that global demand for natural, sustainable and renewable products was growing at a rapid pace, noting that wood fibre was the perfect source material for such products, with dissolving wood pulp, or specialised cellulose, being one such product.
“With a very wide range of uses, the product is in high demand,” he commented.
Specialised cellulose could be used in products such as textiles, personal beauty products, and hygiene products, in addition to having medical and industrial uses.
The major aspects of the GoCell project included the construction of the new fibre line comprising a batch pulping plant, washing and screening plant, bleach plant, chlorine dioxide plant, demineralisation plant and a complete chemical handling system.
Further, the number two digester and screening plant was modified into a high kappa pulping facility, and the original bleach plant was decommissioned.
The project also included major upgrades to the number three pulp drying machine, which included a new shoe-press, various wet-end upgrades and a new dryer, as well as upgrades to the bailing line.
Meanwhile, a new hardwood chipping line with log washing was also installed, together with substantial changes having been made to chip screening and softwood chip storage and handling facilities. The old number one fibre line, which used to produce high kappa pulp for the kraft linerboard machine, had also been decommissioned.
Changes were also made to the mill to improve its environmental footprint. These included the replacement of the old bleach plant with a new plant that is much more efficient in respect of chemical consumption and specific effluent discharge, and an improvement in the mill’s energy efficiency with the consumption of coal estimated to decrease by 61 000 t/y.
This reduction equated to 120 000 t/y less carbon emissions.