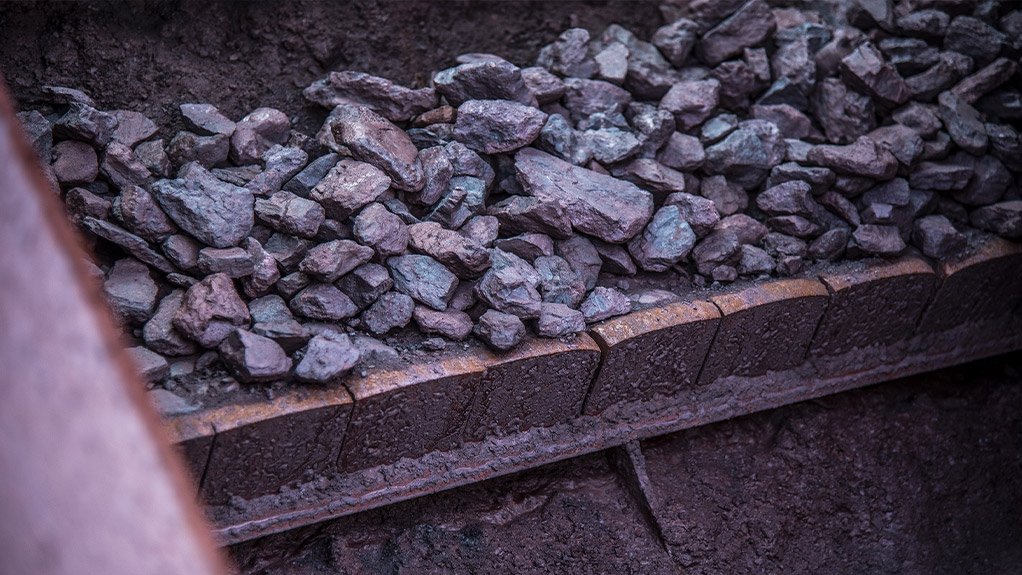
A view of the inside of the chute showing the lips
(Virtual Showroom): The crucial task of transfer chute monitoring has just taken another step into the digital age with Weba Chute Systems’ dedicated mobile app for capturing wear data and other key indicators in real time.
Izak Potgieter, ISO systems manager at Weba Chute Systems, highlights that a key factor in the company’s leading role in chute technology is its ability to track wear and predict maintenance requirements.
“In recent years, we have fine-tuned our reliability model so that we give customers regular and detailed updates on the condition of their chutes,” says Potgieter. “This cuts plant downtime and improves productivity, as we reduce any possibility of unscheduled disruptions.”
Weba Chute Systems’ reliability model takes data from its regular inspections by its teams – such as tonnages through the chute and wear on components like lips and liners – and calculates wear rates. In turn, these wear rates allow the company to forecast when maintenance needs to be conducted, and on which particular components.
“The Android app that we have put into action this year further enhances the value of our reliability model, by speeding up data capture so that wear information is available almost in real time,” he says. “Vital data like throughput tonnages and wear measurements, as well as photographs, are entered into the mobile app at the time of inspection and are uploaded directly to the reliability model.”
The removal of ‘hard copy’ methods of data collection, which would require manual recapturing into a digital format, means that data capture can be quick and seamless. The app has been efficiently designed to prompt the user with each aspect of data required. Even the related photographs can be taken on the user’s mobile phone, creating visual evidence to enhance the statistical basis of the model.
“Our team member inspecting physically measures the wear on each necessary point, and also enters operating data from the mine on aspects like belt speeds and tonnages,” he says. “They will also add their own comments and recommendations for each chute.”
By flagging any changes in the expected wear rate, Weba Chute Systems’ reliability model can adjust for modified conditions – such as higher tonnages – and recalibrate the wear predictions for maintenance purposes.
“Our monitoring app allows the reliability model to be quickly updated, so that we can timeously generate a customer report on each chute,” says Potgieter. “The sooner the mine can be informed of their chutes’ condition, the better.”
The frequency of inspections depends on the chute’s application, with the higher wear applications being required to be checked more often. By streamlining the data capture process and data flow to the customer, efficiency is paving the way to better decision making, he notes. This is especially the case when Weba Chute Systems has up to 50 chutes on a single site.