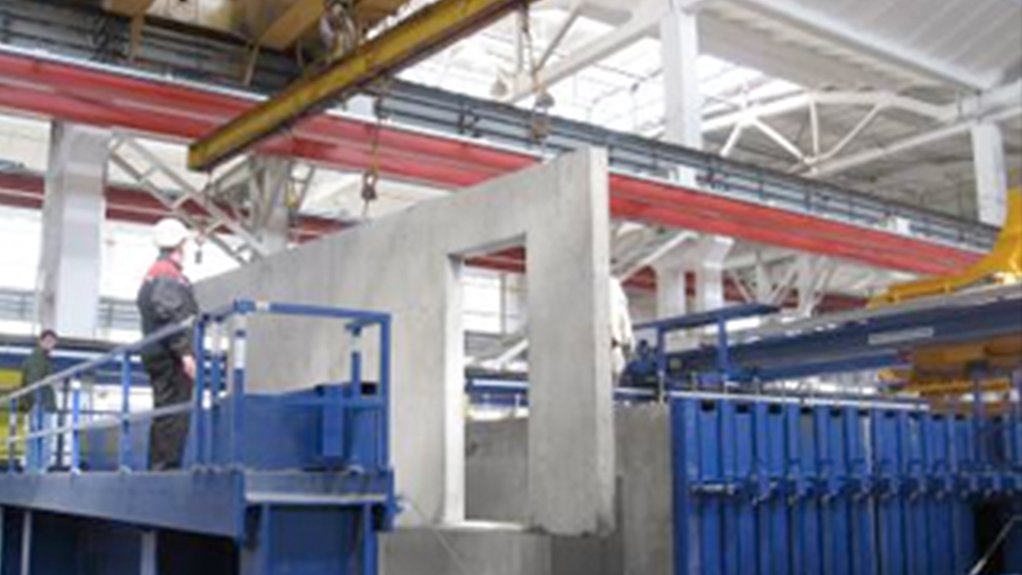
STATIONARY BATTERY MOULD Weckenmann Anlagentechnik developed a mobile formwork for the vertical manufacturing of flat precast concrete elements
As a result of demand for faster construction of large residential complexes to meet the need created by rapid population growth and urbanisation, the use of precast concrete elements is growing, says concrete elements production plant manufacturer Weckenmann Anlagentechnik.
The company notes that, in light of these factors, transport of concrete elements from central precast plants is too time consuming, with the added risks of the products being damaged or delayed during the transport period.
In addition, stationary precast plants require large-scale investments, which are frequently not realised owing to a lack of funding or a long-term, secured market.
In response to these factors, Weckenmann Anlagentechnik developed a concept of mobile formwork for the vertical manufacturing of flat precast concrete elements two years ago.
The Mobile Factory
The company’s idea is based on the concept of a battery mould mounted on a special vehicle, like a semitrailer, that can be hauled by conventional tractor units. This special vehicle can be used for the transport of the heavy, central and external shutters. Additionally, the vehicle can act as a central assembly platform on a building site to which further work platforms can be attached.
These additional working platforms, as well as the intermediate forms and other small-scale equipment components, will be transported by conventional vehicles from construction site to construction site.
In addition to this mobile battery mould system, a suitable lifting gear is also required for the assembly of the battery mould. The lifting gear can then also be used for all the other load movements necessary in the ongoing production process, such as the removal of the form, the reinforcement installation and the concrete placement.
If required, the system can be complemented by a heating unit, which is fuelled by oil or gas, and provides the battery mould with hot water.
Extensive market and feasibility studies ultimately confirmed the enormous potential of this new concept, Weckenmann Anlagentechnik says.
The Battery Mould
The stationary, vertical mould, which is mounted on the vehicle, is notable for its easy manufacturing process, compact design and energy efficiency.
The highly-effective, compact equipment guarantees that the end product is impervious to varying concrete qualities while the design ensures a high output with a relatively low footprint.
The battery mould consists of a fixed central part, two mobile external shutters, several mobile, intermediate shutters, and adjustable vertical side and horizontal base shutters, depending on the thickness of the element.
There are electric vibrators, powered by a frequency controller with adjustable speeds for optimum compaction performance, which are integrated into the form panels, along with a heating element that ensures fast hardening, and a hydraulic unit and two hydraulic cylinders for the safe and tight sealing of the mould.
Transportation and Assembly
A plane and horizontal site with adequate load-bearing capacity is the precondition for setting up the mould system, the company says, adding that individual simple spot footings for supporting the special vehicle and the attached working platform might also be required.
The special vehicle is brought into position and levelled; then the working platforms are delivered, mounted and adjusted. Afterwards, the remaining components of the battery mould are set up. The battery mould can be put into operation immediately after the connection of the energy supply.
Implementation
Two building contractors from Singapore independently decided to use this new technology and the plants were put into operation in the second quarter of 2015.
The use of the mobile battery mould is expected to offer great possibilities for the city State and its 5.5-million inhabitants at the southern tip of the Malaysian peninsula.
On the one hand, the city is shaped by brisk building activity in which fast construction progress is important and high productivity is demanded and funded by the State. Achieving that necessitates the consistent use of precast concrete elements.
On the other hand, this small 712 m2 island offers little space for industrial settlements where precast elements can be produced in a plant.
Weckenmann Anlagentechnik will take full advantage of the opportunity to infiltrate the African market by attending the BAUMA CONEXPO AFRICA at the Johannesburg Expo Centre from September 15 to 18.