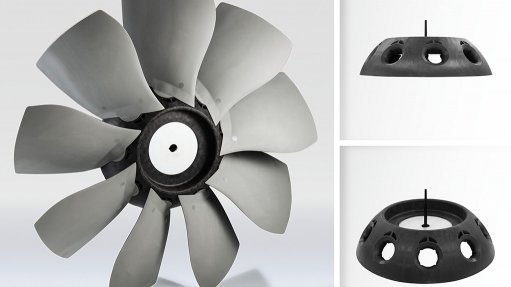
FIBRE-GLASS REINFORCEMENT BASF’s new long glass fibre-reinforced polyamide Ultramid Structure B3WG10 LFX is used in the production of mixed flow fan hubs
Denmark-based axial impellers developer Multi-Wing International A/S has been using chemical company BASF’s new long glass fibre-reinforced polyamide Ultramid Structure B3WG10 LFX material in the production of the hubs of its new mixed flow fans since January, when the product was introduced onto the market.
BASF engineering plastics application developer Andre Schäfer explains that the hubs are circular parts fitted on axles or pulleys that transfer the circular motion to the fans, adding that fan impellers are used in ventilation systems such as tunnel ventilation systems, engine cooling systems and air-conditioning systems.
“The new BASF polyamide fibre system improves bonding within the plastics, which results in a more stable fibre skeleton structure.
“Key features of the material are its good weld line strength and creep resistance, particularly at high temperatures, which make it ideal as a substitute for metal,” says Schäfer.
Subsequently, the material can withstand the extreme stresses that axial fans are subjected to, such as high speeds and natural oscillations and vibrations. This further enables the polyamide fibre system to provide protection against damage and excessive deformation of the plastic, with the system’s high-notched impact strength also allowing for impact and shock-energy absorption at down to –30 °C without breaking.
Schäfer notes that the plastic also has good heat resistance and retains its mechanical properties over a wide range of temperatures and, as a result, exhibits good, long-lasting dimensional stability even at elevated temperatures.
The Ultramid Structure LFX is easy to process and ensures trouble-free production, making it a versatile material to use, he says, adding that BASF has optimised the material’s properties to such an extent that it has proven to be a good investment in several applications and projects.
“The material can withstand extreme centrifugal forces. The stable fibre network makes it ideal for heavy loads and, therefore, a good alternative to metals in the production of our hubs,” says Multi-Wing International A/S development manager Victor Silbermann.
Schäfer says BASF performs about 15 to 20 different mechanical tests to assess the performance materials. The company regularly performs tests for each production lot to ensure quality at all times.
He says the Ultramid Structure LFX portfolio, together with speciality polymer grades, is available in commercial volumes and with detailed material data.