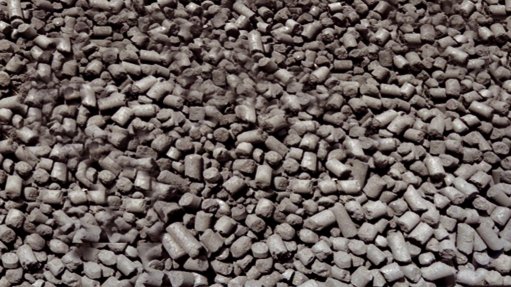
COMBUSTIBLE MATERIAL John Thompson carries out tests on a variety of biofuels, including torrefied biomass owing to growing demand for a cleaner and sustainable environment
Owing to the price of biofuels becoming more competitive than that of traditional fuels, such as coal, oil and gas, the need for biofuel-fired boilers is steadily increasing, says Cape Town-based industrial boilers manufacturer John Thompson divisional technical manager Etienne de Villiers.
He notes that, with biofuels being produced regularly through farming, the manufacture of biofuel-fired boilers will also help reduce carbon emissions.
In response to the growing demand for a cleaner and more sustainable environment, and the verification of boiler design and combustion parameters, De Villiers says the company conducts tests that entail firing a variety of biofuels.
Tests on biofuels are normally conducted at the premises and on behalf of clients who want to use them as an alternative to coal, oil and gas, as well as on the Europac boiler installed at John Thompson’s boiler development and training centre in Bellville, Cape Town, he explains.
De Villiers adds that the tests are carried out on wood pellets, wood chips, wood pucks, grape pomace, nutshells, sunflower seed husks, corncobs, dried hops and torrefied biomass.
The torrefaction of biomass is a mild form of pyrolysis at temperatures typically between 200 °C and 320 °C, and it changes biomass properties to provide a much better fuel quality for combustion and gasification applications.
De Villiers tells Engineering News that the company is also working on the large-scale manufacture of torrefied biomass pellets, which is a form of charcoal.
The torrefied material is produced from woody biomass through controlled pyrolysis to produce a friable material that can easily be pelletised. This product has a calorific value and volatile content comparable to coal, but does not contain any sulphur and has a lower ash content.
Several industries use steam as a heating medium and the most cost-efficient fuel currently available for firing boilers is coal, which, in turn, requires expensive pollution control systems to reduce particulate emissions, he says.
However, De Villiers highlights that the production of torrefied material is a viable and competitive alternative to coal and promises to mitigate costly pollution control system expenses.
He notes that torrefaction provides a method of beneficiating woodchips and other woody biomass as a fuel by increasing the energy density of the material. This reduces the transport costs involved in moving renewable biofuels over long distances from source to end-user.
Producing torrefied material will lead to an alternative fuel to coal for industrial boilers, such as John Thompson’s Europac package firetube and MicroGen cogeneration water- tube designs, De Villiers concludes.