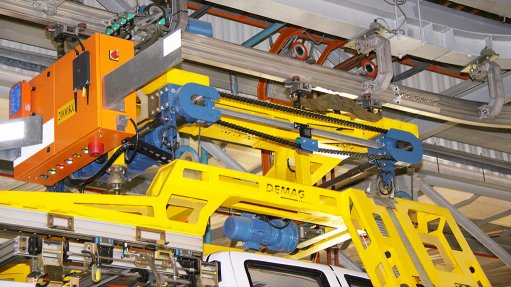
DEMAG MONO-RAIL SYSTEM South Africa’s automotive industry has a specific need for robust and heavy-duty linear overhead materials-handling solutions
South Africa’s automotive industry has a specific need for robust and heavy-duty linear overhead materials handling solutions, which has seen specialist crane and related components manufacturer Demag Port Elizabeth supplying its Demag Monorail System (DMS) to the industry, with DMS having been developed specifically as a modular solution to meet this customer requirement.
“When we initially designed the system, we were looking to cater for increased throughput in terms of cycle times, taking safe working loads into account,” says Demag project engineer and technical sales representative Niki Mizen.
Demag Port Elizabeth’s first major international customer was General Motors (GM) Egypt. Mizen notes that, when the GM global operation heard what the company had achieved in South Africa, it directed an enquiry to Demag from the Middle East for a specific turnkey solution.
“The fact that we can carry out complete turnkey projects means that Demag Port Elizabeth is in the unique position of being a one-stop shop,” adds Mizen.
He notes that the company’s DMS solution, which is locally manufactured to European standards, complements its KBK light-crane system, which comprises suspension monorails for overhead materials handling requirements. The main features of the DMS solution include ease of installation, owing to light aluminium construction; silent and smooth operation from polyurethane wheels running on aluminium, with no metal flaking; high transfer speeds; accuracy of positioning; and low maintenance and running costs.
“Our success with the system over the past decade has marked our long-term involvement with many of the major automotive original-equipment manufacturers in South Africa,” notes Mizen, adding that the company’s success is largely attributable to its focus on being innovative and flexible.
Mizen adds that the system’s low-maintenance requirements are a result of no metal-to-metal contact on any moving parts. This, in turn, enhances the robustness of the entire system. Further, the aluminium system uses polyurethane tyres to prevent metal-on-metal flaking.
Another feature of the DMS is that it can be fully or partially automated. Demag can supply a total solution for any components that need to be picked up and for any end products that need to be transported or assembled. DMS is fully customisable, using specific branded components required by the end-user, such as switchgear and programmable logic controllers. The industrial wireless communication allows for seamless integration between the hoist and the main control panel.
As a result of the DMS being a modular system, it is flexible enough to cater for a range of parameters. Such modularity also allows for easy transport or shipping using 12 m shipping containers. This is a solution-orientated system that can be designed to fit into any factory layout.