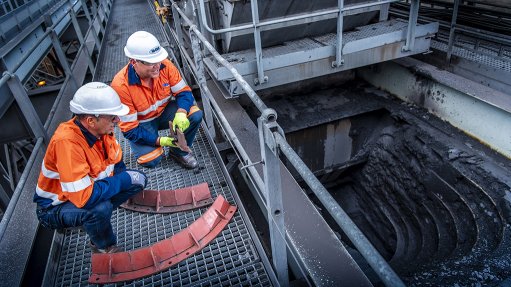
Weba Chute Systems’ reliability model helps improve uptime in plants
A new reliability model developed by Weba Chute Systems aims to help customers improve plant uptime and facilitate planning.
The tool enables users to capture, store and calculate vital information about wear rates on different components within individual chutes.
“The data specifies exactly which chute is being referenced, where it is physically located in the mine or plant, the components it includes and the dimensions of these components,” says Weba Chute Systems ISO systems manager Izak Potgieter. “Data is captured over time on the tonnages that pass through the chute, and the wear that occurs on components such as lips, liners and dead boxes.”
When inspections of the chute are conducted, precise measurements are taken of wear levels so that comparisons can be made over time. The tool generates important calculations such as the wear rate per hour or per day, which allows forecasts to be made about key indicators such as mean time between failures.
“By applying the concept of exponential distribution to the percentage reliability required by the customer, we can then calculate the number of hours that the chute should be able to operate between maintenance interventions,” he says.
Average tonnages passing through the transfer point are usually gathered from the mine’s supervisory control and data acquisition, or SCADA, system. If these tonnages – or the nature of the material – does not change, then it should be possible to reasonably accurately predict the wear life of each chute’s various components.