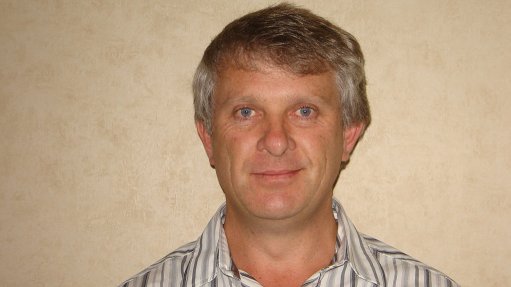
WYNAND MARX The priority is to capture or convert most of the pollutant at or near its source, with ventilation used to dilute the remainder
In South Africa, there is an increasing move towards mechanisation, which leads to more extensive use of diesel equipment in underground mines. Diesel equipment can, however, introduce health risks from heat, exhaust gases and diesel particulate matter (DPM).
In 2012, DPM was declared a confirmed human carcinogen by the United Nations’ World Health Organisation’s International Agency for Research on Cancer.
While various efforts have been made by the Department of Mineral Resources (DMR) and the mining industry to determine an acceptable concentration of DPM that could be used as an occupational exposure limit, no legally binding standard has yet been put in place for DPM.
The DMR is, however, introducing an interim DPM exposure control value using a phased-in approach, which the department aims to gradually lower over the next few years.
Recent statements have indicated that the first interim target may take effect at the end of 2014 – a level which is expected to be comparable to the interim targets used by developed countries, says ventilation and refrigeration consulting engineering firm BBE Consulting MD Wynand Marx.
He says the mining industry has relied on implementing best practices, such as engine exhaust control measures and mine ventilation systems, to control DPM concentrations in underground mines. “As with controlling any pollutant, the priority is to capture or convert most of the pollutant at or near its source, with ventilation used to dilute the remainder,” explains Marx.
“DPM exposure control can be achieved using modern high-tier engine technology, high-quality low-sulphur fuel and exhaust filtration technology, as well as by performing regular and thorough maintenance on the vehicles. Mine ventilation is implemented to dilute the remnant DPM at the point of use underground.”
It must, however, be highlighted that the necessary engine technology, fuel specification and maintenance skills are not yet readily available in South Africa, which hinders the implementation of engine exhaust emissions control measures, Marx points out, adding that dilution of DPM using adequate mine ventilation is currently the most common method applied.
Application of other technologies, which generally requires ultralow sulphur fuels, are available now in some areas but is scheduled for national availability in 2017, says Marx.
Mine ventilation practitioners are implementing a step-by-step mine ventilation process at mines to mitigate occupational exposure to DPM.
The first step is to generate a ‘working-vehicle’ inventory of the actual underground vehicles at the mine, as well as the emissions and usage characteristics.
The mine ventilation practitioner will then analyse the data, conduct risk assessments and identify hazardous exposure groups, including other toxins and heat.
Thereafter, the required ‘diesel dilution’ ventilation rates must be identified, as well as any exhaust emissions control measures.
Marx explains that after implementation, it is important that the emissions quality of underground vehicles is monitored on a regular basis as part of the maintenance procedure once the vehicle is redeployed.