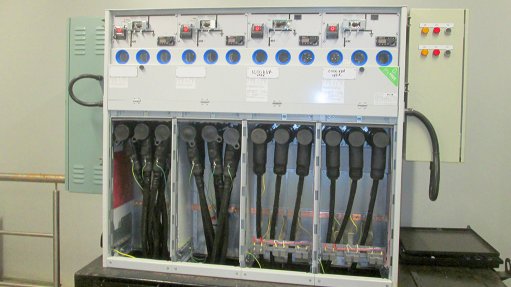
Medium voltage compact switchgear with ring main unit, battery tripping unit and metering panel.
Three transformers were recently designed, supplied and commissioned for a global beer maker’s expanded facility in Gauteng. These included a 1 250 kVA and a 1 600 kVA unit, both with 11 kV to 400 V capacity, as well as a 2 000 kVA unit for 11 kV to 690 V application.
Dry-type transformer supplier Trafo Power Solutions delivered the transformers and other electrical upgrades to the facility. As part of the project, the company was required to liaise with the customer’s Europe-based engineering team as well as with local electrical contractors and consultants.
The transformers were designed to meet the customer’s specific requirements, which included compliance with the European Directive on Efficiency and optimising energy efficiency. To this end, Trafo asserts that it was able to supply the lowest-loss dry-type transformers available.
Also supplied was medium voltage switchgear, including two ring-main units (RMUs) with one a three-way and the other a four-way.
The RMUs were modified in line with the customer’s requirement, including a battery-tripping unit on each unit, aimed at ensuring the availability of power regardless of the condition of the circuit breaker.
As a brownfield project, there was considerable adaptation of design to suit the plant configuration. Instrumentation was located on a raised base, for instance, where voltage transformers and current transformers were installed for monitoring each RMU.
In addition, three specialised distribution boards (DBs) were installed between the low voltage transformers and the new sections of the plant and new brewhouse, explains the supplier. The non-standard design was created as a modular-type assembly conforming to EIC 61439 and EIC 61641 certification.
The DBs were designed to provide the highest level of safety and were fully-tested for IEC 61641 , or Internal Arc Fault, compliance and incorporate 2 500 A incomers, distributing through various feeder circuits to the rest of the plant. Two of the DBs are 400 V and the third is 690 V. Another non-standard aspect of the DB supply was its Form 4A design, so that each compartment is separate, explains the company.