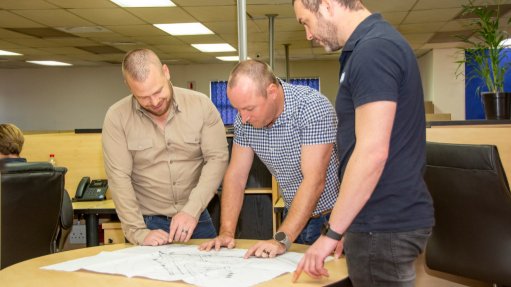
OPEN COMMUNICATION Turnkey projects demand clear channels of communication and agreement with the customer on a regular meeting schedule to ensure that all stakeholders are kept informed throughout the project cycle.
With the promise that its customised transfer point solutions will always perform to expectations, transfer chute technology provider Weba Chute Systems tackles its turnkey projects in a highly systematic and controlled manner.
The company has successfully carried out more than 25 turnkey projects in the past decade, including contacts in the mining, steel, ports and food industries, says Weba Chute Systems project manager Ted Cruickshank.
Among these substantial projects was the design, manufacture and installation of 36 chutes at a steel maker’s sinter plant in South Africa, and 11 chutes for a project house developing a mine in Zambia.
“More recently, we completed a turnkey project for [several] crusher chutes at a platinum mine in Zimbabwe,” Cruickshank says. Further afield, Weba Chute Systems provided chute designs to accommodate a three-way conveyor in an operation in Trinidad and Tobago, which is awaiting execution.
Attention to Detail
“It all starts with defining the project’s objectives and scope. This is followed by establishing the budget so that an accurate quotation can be prepared, as well as planning a timeline that meets the customer’s schedule,” explains Cruickshank.
He emphasises that turnkey projects demand clear channels of communication, so a regular meeting schedule is agreed with the customer to ensure that all stakeholders are kept informed throughout the project cycle. This is particularly important for dealing timeously with issues so that the project’s progress is not unduly impeded.
“On some projects, we can work off the customer’s drawings, but we often go to site to conduct our own surveys, on which we base our calculations and designs,” elaborates Cruickshank. Chute flow designs and layouts are then completed and approved, followed by fabrication approvals, all within a stringent quality control plan (QCP).
He states that the company’s efficient procurement allows fabrication to get under way without delay, and stringent quality checks are carried out at every stage of manufacture.
Cruickshank emphasises that rework needs to be avoided if projects are to run on-time and on-budget, and this means stringent quality control. Weba Chute Systems uses ISO 9001-2015 as the standard to document and control all quality-related activities.
“Regular audits and certifications help maintain a high level of consistency in the quality of our products across all projects. Quality inspections at different project locations ensures that the equipment adheres to the project’s quality standards,” he states.
Risk Mitigation
A risk assessment on each project identifies all potential hazards and forms the basis for mitigation plans. There is also growing pressure on mines and their contractors to minimise environmental impacts.
“Noise, dust and spillage are among the main environmental risks associated with transfer chutes. We mitigate these impacts through optimising the flow dynamics in our tailored chute designs – accommodating the specific conditions of each application.”
Cruickshank adds that this includes understanding the material characteristics and particle size distribution, as well as flow rate, trajectory, velocity and points of impact.
Optimised material flow decreases the turbulence at the transfer point, in turn reducing dust and noise. Smooth transfer of material to and from conveyor belts also cuts the spillage and improves health and safety conditions around the belts.
He highlights the value of project planning software to plan and monitor progress during turnkey projects. These tools enhance real-time collaboration and efficiency, with other enabling technologies including three-dimensional modelling and data management.
“We also use video conferencing and cloud-based document handling to streamline our communication with customers and other parties to the project. This improves overall efficiency and resource coordination,” he explains.
Cruickshank concludes by highlighting the value of local suppliers, engineers, and partners in the country where the turnkey project is being executed, adding that Weba Chutes Systems prioritises these links by building positive long-term relationships with local partners to overcome potential barriers of culture, language, lead times and cost efficiency.