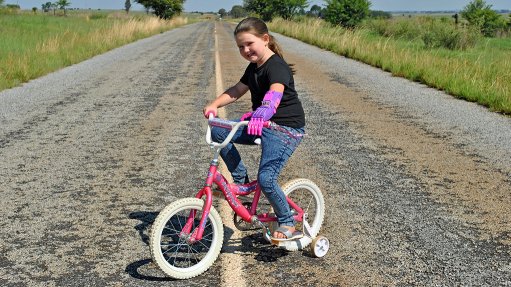
MEAGAN VAN DER MERWE Van der Merwe with her 3D printed left hand, which used an open source design
A partnership between engineering and technology firms is being leveraged to test the design, suitability and production of affordable prosthetics for Africa using three-dimensional (3D) printing, says 3D design technology firm Solid Edge Technology business development manager Jared de Waal.
The company is involved in the design, printing, testing and modification of a 3D-printed prosthetic hand and forearm for a six-year-old girl Meagan van der Merwe, who was born with symbrachydactyly, which resulted in her left hand not developing fully. Van der Merwe requires a new prosthetic hand every 18 months as she grows, similar to conventional prosthetics.
The costs of conventional prosthetics are estimated at R200 000.
“However, the ability to print external body parts within a short time – 24 hours in this case, and at such a low cost of R1 000 for the materials – means that this technology can be a real solution for many people across Africa,” says De Waal.
Solid Edge Technology partnered with information technology systems distributor Rectron and 3D printing equipment manufacturer MakerBot to produce the prosthetic.
“Printing a limb was a new challenge for us. The first step for us was to find the right links to the files we would need to print a suitable hand for Meagan. Fortunately, the 3D printing ecosystem makes many of its designs public,” says De Waal.
The team used Siemens Solid Edge with synchronous technology to convert the open-sources files to a native format that it could use. To ensure the hand it printed would be the right size, the company took a measurement across a section of her hand, which was applied to a calculation to scale the original design.
The company then printed a prototype, which was fitted to Van der Merwe to test its functionality and comfort. The prototype was printed in her preferred colours – pink and purple – and De Waal and his team assembled the hand, comprising 12 unique parts and 31 individual 3D-printed components using a MakerBot 3D printer.
“Solid Edge Technology decided to approach Meagan’s case as a lifetime case study, whereby we will replace the hand or its parts and customise as necessary while using this as an opportunity to gain knowledge and experience on a new and exciting application of 3D printing.”
Part of the project is to observe how Van der Merwe uses the existing design and then to improve its functionality over time. Further, the company gave her parents permission to adapt and modify the hand to make it more comfortable as needed.
“We adjusted the strings of the hand so that it grips better and we replaced the Velcro strip with a bigger one to keep the hand more securely on Meagan’s arm. We also got her a leather sleeve to protect her arm from bruising,” De Waal explains.
Based on the positive impact this has had on Meagan’s life in a short time, her parents and De Waal believe that 3D printing technology can benefit others with similar disabilities across Africa.
“At this point, it is about learning how far we can push the hardware.
“It is an exciting project to be involved in – using premium products and the latest technology, and working as a community with like-minded brands to make a real difference,” he concludes.