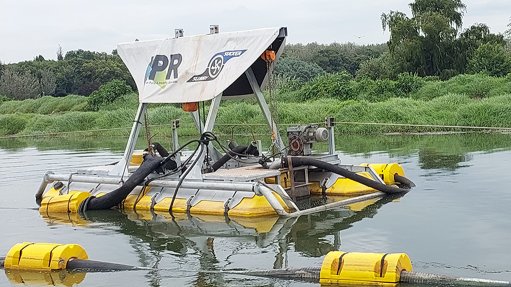
The SlurrySucker MK III pump from IPR
A newly launched dredging system is described as the most efficient and cost-effective electrically powered floating dredge system currently available.
The locally manufactured SlurrySucker MK III from IPR is used to clean process water ponds, return water dams or other water storage areas and is said to be an ideal solution for cleaning water capture areas where silt is an issue, or where water retention and water holding capacity is being threatened.
IPR MD Lee Vine says that the benefits of the new generation SlurrySucker extend well beyond improving mines’ environmental footprints. “Bodies of water such as ponds, lagoons, dams and canals should be considered valuable plant assets and must be maintained to maximise their operational efficiency and contribution to optimised operational performance,” he explains.
“This is where the SlurrySucker has continued to deliver without fail, assisting our customers with some of their pressing issues, including the need to increase water storage capacities, the recovery of minerals and improving process water quality,” he continues.
Equipped with Toyo heavy duty slurry pumps, the units are fitted with robust cutter fans or agitators, facilitating the management of larger particles. The pump boasts enhanced solids handling capabilities and is designed to effectively handle slurries with a high specific gravity.
The unit can be sized to meet an individual plant’s slurry removal requirements in terms of particle size, aggregation, distribution, cohesiveness, flow characteristics, sedimentation rates and specific gravity.
“Historically many operations have used manual excavation methods for desilting and cleaning, but our established track record has proved that this is not only inefficient, but it often fails to remove the required volume of sediment,” Vine says.
There are several ways to accomplish effective desilting, but the best option, according to Vine, is ascertained through a site visit to assess the application requirements and conditions.
“In some instances, it is possible to pump the high solids material to another nearby dam or reservoir. However, this is sometimes not possible and in this type of scenario we implement an alternate solution such as capturing and storing the content in specialised geotextile bags while the water is separated from the solid material,” he explains.
Vine highlights two product options, namely the Maxi SlurrySucker which is capable of moving 250 m³ an hour at 20% to 30% by volume – equivalent of approximately 70 dry tons per hour, and the Mini SlurrySucker which operates at 100 m³ an hour, at 20% to 30% by volume for roughly 30 dry tons every hour.
The SlurrySucker comes standard with a galvanised frame structure and the option for stainless steel with polyethylene and ultra violet-stabilised pontoons. An added safety feature is the remote operation of the unit, allowing the barge to be operated away from the dam or pond edge.