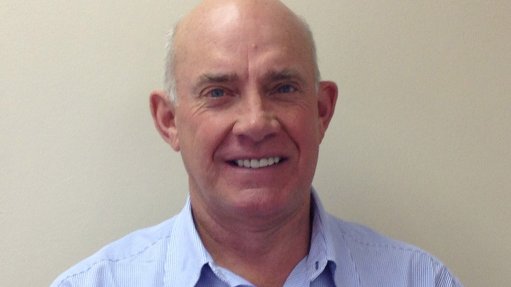
CASSIE LESSING StratoPod dramatically decreases the incidents of claims and can be integrated into document management and enterprise resource planning systems
South African information technology (IT) business solutions company Strato’s newly launched electronic consignment management and verification system is helping to reduce costs and claims in the logistics and delivery industry, says Strato IT MD Cassie Lessing.
The StratoPod proof-of-delivery system uses smart devices, typically tablets, that hold the consignment information and are also used to capture the signature of the receiver once it is delivered.
The exact quantities of goods are reflected on the devices and digital copies of the invoice, while delivery notes are sent to all the relevant parties, such as the supplier, the delivery company and the customer, once the consignment has been delivered.
“The aim is to eliminate the problems and losses that occur as a result of traditional paper-based delivery notes and enable immediate notification of damages or problems such as incorrect quantities of goods to be captured.
“As the devices also have cameras on them, any damaged goods can be photographed and the information immediately sent to the relevant parties, with changes instantly reflected in inventory and delivery systems, and credit notes sent,” explains Lessing.
A positive outcome of StratoPod is that it has dramatically decreased incidents of claims of companies using the system. The delivery vehicle and its movements are also tracked, improving management of turnaround times and helping to prevent loss of goods, including those returned.
The StratoPod system also serves as an effective tracking, tracing and delivery turnaround management system, as the devices are geolocated and the exact times of delivery captured.
“The benefits of accurate information of all aspects of deliveries are significant and these extend to cross-border deliveries, where costs of delays, returns and disputes are high. The system works even without constant connectivity, as the data is uploaded once connectivity is established,” explains Lessing.
Lessing notes that the information captured by the proof-of-delivery system can be integrated into document management and enterprise resource planning systems and, thus, support near-real time enterprise management and oversight.
Logistics managers can use the virtual dashboard – an online system management tool – to manage and monitor all the devices and, hence, deliveries made using the system.
Lessing highlights that the company has implemented the system for Toyota South Africa, specifically for its parts distribution network. Parts distribution is often very complex and fraught with inconsistencies and disputes. However, Toyota South Africa has reported that it has significantly improved the accuracy of its parts distribution using the system.
“Having such a large multinational client as a customer is a significant boost for us, but a key strength that we draw from our internal development is the ability to design each system to match the requirements, and iterative changes over time, of each customer’s delivery and logistics operations.”
The company provides design support and advice services for clients, which enables them to change and add functionalities to their systems, as demanded by the clients, concludes Lessing.