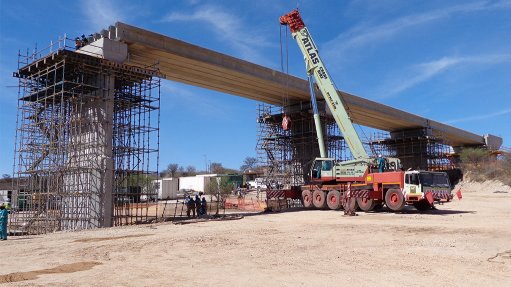
RAILWAY SIDING PROJECT GIBB is undertaking the engineering and construction monitoring contractor for the 20 km Kalagadi Manganese railway siding
South African consulting engineering firm Gibb is undertaking construction monitoring services during the 18-month-long construction of the 20 km Kalagadi Manganese railway siding project, connecting the main manganese corridor at Hotazel, in the Northern Cape, to the Port of Coega, in Port Elizabeth.
Gibb was appointed in 2010 as the engineering and con- struction monitoring contractor for the project.
The railway siding will enable Kalagadi’s mine to export manganese ore (sinter) through the Port of Coega. The railway line will also be used to import coke for the beneficiation process.
The railway siding consists of an electrified and signalled running line with a balloon configuration of 12 km. Yard 1 consists of 3.4 km of electrified lines and Yard 2 of 4.1 km of unelectrified lines.
“The yard layout consists of a balloon for the rapid loading of the sinter product, a linear yard for the tippler offloading of coke, a yard for shunting movements and a locomotive shed for light maintenance,” says Gibb rail technical executive Wimpie Oosthuizen.
The mine will produce 2.4- million tons of sinter products, of which 71% will be sold to the export market through the Port of Coega. The remaining 29% will be beneficiated in the Coega industrial development zone to produce ferromanganese.
The mine will create about 1 000 permanent jobs in Hotazel and 300 in Coega, while the project in its entirety will support about 8 800 direct and indirect jobs in the Northern Cape and 5 500 direct and indirect jobs in the Eastern Cape.
One of the major challenges on the project was to find suitable construction material for the bulk earthworks, which include fills, pavement layer works and a service road. “The importing of calcrete material from the neighbouring mine and using discarded rock material from the mining activities resolved the major problem of obtaining good construction material.
Further, Oosthuizen says three design issues relating to the site conditions were encountered and subsequently resolved through the innovative use of material.
“As a result of the challenge of obtaining construction material, one of the pavement layers that required material from a commercial source was changed to use the abundant calcrete material. The calcrete material was processed with 3% cement to provide the same structural requirement as the imported material,” he says.
He further explains that the second design element issue was that Kalahari sand is highly collapsible when loading is increased and water is added.
As a result of this, the predicted subsidence was more than the allowable specification and the design to mitigate the potential collapse/subsidence of the soils entailed excavating the material by 500 mm and wetting and compacting the on-site material with a three-sided impact roller.
Oosthuizen explains that the on-site material was then strengthened by placing a 500-mm-thick pioneer layer on top of the on-site material that formed the foundation for the bulk fills.
The third and final design element challenge was that the traction substation was changed from a traditional brick building to a containerised solution.
Oosthuizen maintains that this provided a total off-site design, supply and assembly solution. The completed containerised sub- station will then require minor installation works on site and its installation will realise cost savings, compared to the original planned substation.
Gibb expects the project to be completed by the first quarter of 2014.