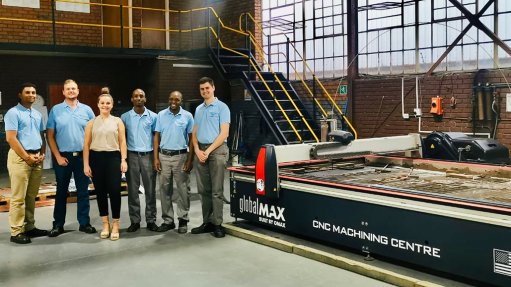
SUSTAINABLE MANUFACTURING MAXJET’s manufacturing processes, which use waterjet cutting to design, supply and process flat part components, is an environmentally green process
Waterjet cutting service provider MAXJET will launch a new manufacturing division, referred to as MAX LINERS, next month.
The division will focus on providing a range of products to prevent wear in the materials handling industry.
“We will mainly supply and stock chromium carbide-clad liner plates (CrC), which are extremely abrasion resistant when compared with general steels. They are manufactured to European standards, with hardness averaging between 600 Brinell and 700 Brinell, and 58 rockwell (RC) to 62 RC,” states MAXJET director Preeshan Naidoo.
While the CrC will be promoted by MAXJET this year, the company also offers other products that are suitable for materials handling, including products with materials averaging a hardness of between 450 Brinell and 500 Brinell, as well as plastics and rubber that would be suitable to these applications.
“This is exciting for us, as we combine new technologies with ‘optional’ materials for turnkey, competitive and efficient supply.”
Further, Naidoo adds that, as a “first in Africa”, this year, the company has accurately processed conveyor rubber belting of more than 100 m long, while maintaining tolerances.
He enthuses that this is a “huge success, and exclusive to MAXJET”.
Green Cutting
MAXJET’s manufacturing processes, which use waterjet cutting to design, supply and process flat part components, is an “environmentally green process”, says Naidoo.
“We use only tap water that is recyclable, with no gas emissions whatsoever. We wish to encourage minimising the carbon footprint of our processes.”
MAXJET’s computer numerical control (CNC) jet machining process, also referred to as waterjet cutting, is a nonthermal cutting method that uses abrasive garnet sand and tap water to cut almost any material.
Tap water is filtered and pressurised in an ultra-high-pressure pump, and then delivered through high-pressure tubing to the cutting head. A small-diameter orifice will concentrate the CNC jet machine, and the pressure transfers into velocity.
The supersonic water stream cuts all kinds of soft material, such as plastic, foam, rubber, composites and wood. This is referred to as cold cutting.
To increase the cutting power, an abrasive medium gets added to the stream, after which the water beam turns into high-speed liquid erosion that an cut through a range of material types.
Naidoo says an environmental advantage of this process is that there are no heat-affected zones when using this process to manufacture components.
This reduces distortions that are formed on the components. The process also reduces dross and splatter that normally collect and are formed from other cutting methods, such as laser cutting, and keeps all intrinsic properties of the component being processed intact.
Minimum waste materials are also produced during this process.
He reiterates that this technology enables the company to process thermal-sensitive materials, such as composites, plastics and rubber, while its US-imported equipment and in-house design equipment have enabled it “to push the boundaries of its capabilities”.