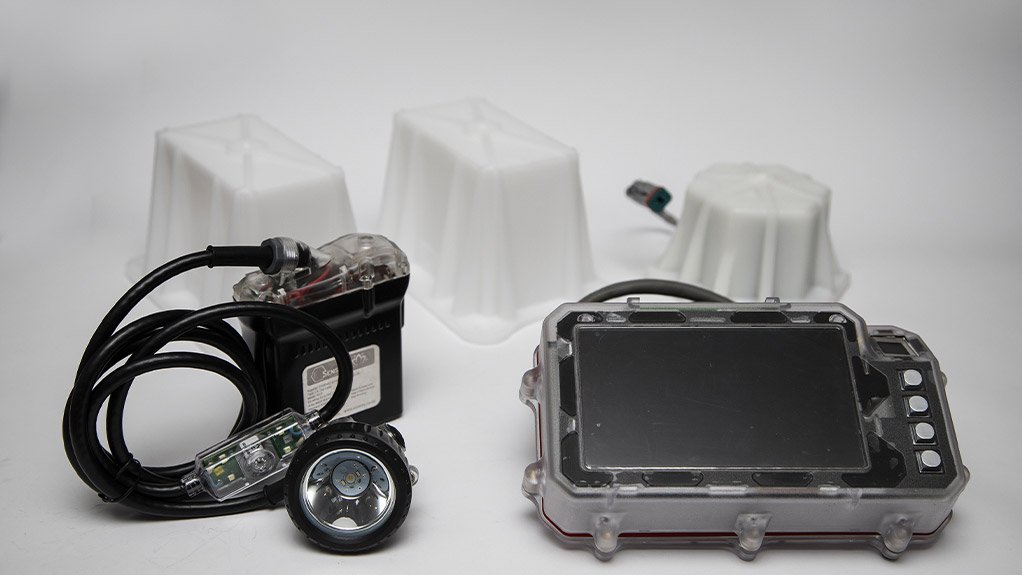
For PDS and CPS systems to effectively reduce risk as they are designed to do, everyone must buy into the project
Putting a proximity detection system (PDS) or collision prevention system (CPS) in place in a mining operation is a process that cannot be rushed, says Anton Lourens, CEO of leading PDS and CPS developer Booyco Electronics.
Rather, it needs solid risk assessment, planning, broad engagement and an integrated approach that considers the myriad details involved. Lourens emphasises that for PDS and CPS systems to effectively reduce risk as they are designed to do, everyone must buy into the project and support its outcomes.
“In Booyco Electronics’ many years in this sector, we generally find that haste is counter-productive,” he says. “Where a safety incident has occurred on a mine, for instance, there may be an understandable impatience to get a PDS and CPS solution up and running quickly. The result, however, is seldom what the customer was hoping for, and the process often just takes even longer than it should.”
The key, he highlights, is to conduct a detailed risk assessment upfront to establish exactly what problems the PDS and CPS are expected to resolve. A successful application of this technology will be one in which the mine is proactive about defining the requirement for PDS and CPS, to make sure they meet the specifications identified in the risk assessment.
The next vital task is to involve all stakeholders, including miners at the coal face, various levels of management, the mine training centre, original equipment manufacturers and other relevant suppliers.
“This engagement – and the acceptance of PDS and CPS by these stakeholders – is vital to a successful roll-out,” Lourens says. “Ultimately, all these parties need to understand why they are installing the PDS and CPS equipment, and what the implications and benefits are for each player in the value chain.”
Machine operators are among the key participants in the process, he notes. They need to engage one-on-one with the teams who conduct the equipment installation, and must receive several rounds of training to understand what the equipment will do and how best to look after it.
“A PDS solution is a potentially game-changing safety device that will reduce the risk of collisions and improve workers’ wellbeing in their daily working environment,” he says. “Over the past decade or more, we have seen industry embrace this technology and put it to good use.”
Nonetheless, he points out that the choice of the right PDS or CPS technology to address the identified risk is still a complex and technical process that needs considerable collaboration between suppliers and mines.