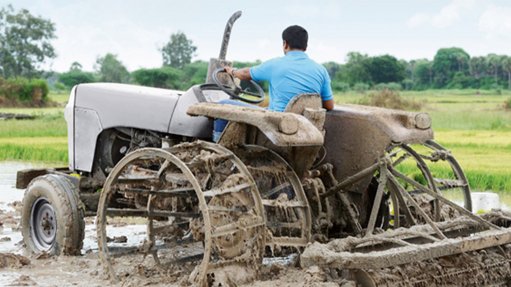
DESIGNED FOR ADVERSE CONDITIONS The saturated, muddy sludge that can characterise Asia’s arable land presents unique performance challenges for electrical and mechanical components
An agriculture industry-based hydraulic system, the Electrohydraulic Hitch Control (EHC-8) from engineering firm Bosch Rexroth, recently underwent enhancements to replicate the same, precise regulation of power and positioning for the lifting and lowering of towed agricultural ploughs for conditions in Asia, and has been delivered to European and North American markets.
Products from Bosch Rexroth are distributed in Southern Africa by hydraulic components and systems company Hytec Group of Companies.
In the transatlantic environments, for which the EHC-8 was principally designed, the product provided improved operation in agricultural applications through a greater control of implement depth, increasing the accuracy of tillage, and turning soils gently and uniformly for improved crop yields.
The same levels of project satisfaction were not, however, originally replicated outside these regions owing to the vastly different climatic and terrain conditions and yields, which led to Bosch Rexroth modifying and re-engineering certain core components and mechanical designs of the EHC-8 to take into account the specificities of Asia’s agricultures.
The first step of tailoring such a solution, thus, was a detailed analysis of the operating conditions. Many regions in Asia are affected by monsoon climates, such as high rainfall and high humidity conditions in which excessively saturated land poses unique challenges to the use of mechanically propelled implements.
The winter months endured by these regions, conversely, present hot, dry and dusty conditions, widening the scope of forces that can be hazardous to equipment components.
Designed for Extremes
During the enhancement process of the EHC-8 for operation in these vastly different conditions, two components in particular required modifications, namely the angular sensor and the control panel.
The control panel was improved for operation in rough terrain, through the application of a protective film, while increased brightness offered greater visibility under intense sunlight.
The control panel was installed in the operator armrest to provide maximum ergonomic operability for improved productivity and operator safety.
Another modification required to enhance the hitch’s viability in these conditions was resistance to leaks. The IP 67 protection-code adhered to in European environments did not take into account the dusty conditions experienced in Asia, requiring a modified sensor and the separation of electrical components from the mechanical space.