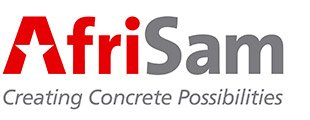
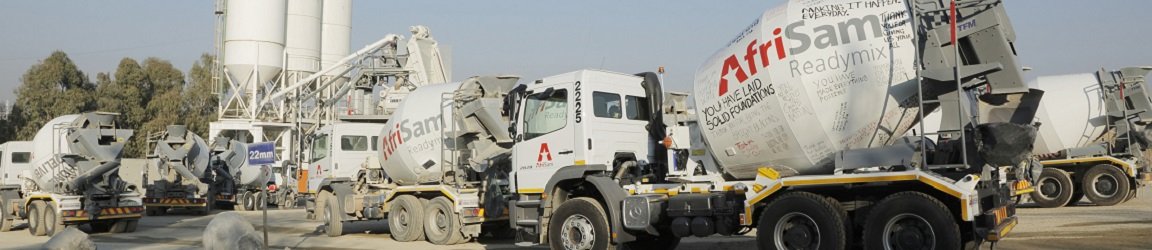
Slag used to reduce clinker factor
According to the Association of Cementitious Material Producers (ACMP), clinker substitution rose from 12% in 1990 to 23% in 2000 and 41% in 2009. Since 2008, the South African cement industry has seen a year-on-year reduction in emissions per ton of cement, largely attributed to the increased focus on clinker substitution.
AfriSam notes that the use of extenders in composite cements has resulted in a substantial reduction in its clinker factor, without compromising the quality of products. Blast furnace slag, a by-product of the steel industry, remains central to the company’s efforts to substitute clinker in its products.
AfriSam has steadily accelerated its efforts to substitute clinker through the development of composite, or extended, cements. In 2000, the company launched Project Green Cement to increase the use of extenders to promote more sustainable products. AfriSam executive: cementitious Hannes Meyer says the use of extenders has resulted in a substantial 20% reduction in the company’s clinker factor since 1990.
Composite cements, he explains, contain not only clinker, but other cementitious materials such as pulverised fly ash from coal-fired power stations and ground granulated blast-furnace slag (GGBS) from steelmaking plants.
AfriSam notes that the use of GGBS product has grown steadily in South Africa and its slagment operation plays a crucial role in the production of its composite cements. The raw material is sourced from steel producer, ArcelorMittal South Africa, which is strategically located some few metres away from AfriSam’s slagment plant.
Blast furnace slag is known for its good cementitious properties, providing enhanced strength and durability. By evolving its chemical and mechanical activation methods, AfriSam says it has achieved a more reactive product allowing the company to progressively replace more and more clinker while retaining high cementitious quality and strength performance.
“Re-using waste products from other industries reduces the amount of limestone that we have to mine and clinker that we have to produce, thus reducing carbon emissions from those processes, as well as minimising waste to landfill,” says Meyer. “We are therefore constantly searching for new extenders and additives to further reduce our carbon footprint and our impact on the environment at large. The end result is less clinker produced per ton of each final product, resulting in less CO₂ generated from our operations.”