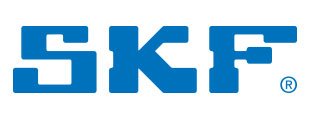
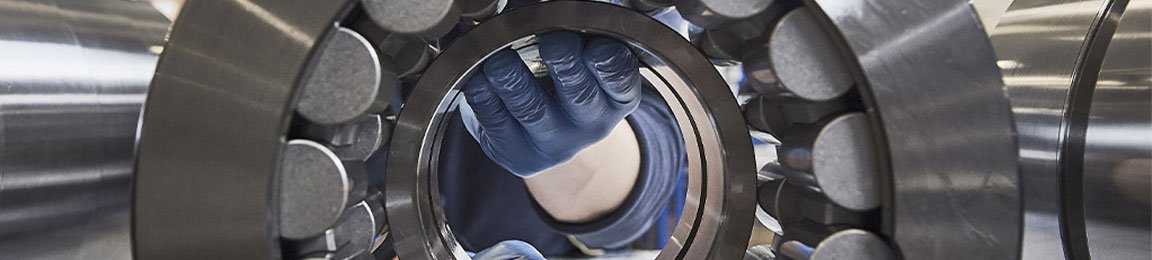
SKF reconditions submerged scraper idlers, more than doubles average Mean-Time Between Failures
The utilisation of SKF sealed bearings, combined with upgraded internal modifications, reconditioning and locally manufactured custom seals, has increased the average MTBF (Mean-Time Between Failures) of scraper idlers on a customer’s Submerged Scraper Conveyor (SCC) from 3-6 months to 12-18 months.
The submerged scraper idlers convey water-quenched, hot coarse ash to the front of the SSC which then collects and dewaters the Boiler Bottom Ash (BBA) before discharging it at a controlled rate onto downstream plant. The SSC’s water-filled top trough, which works in conjunction with the dipper plates, provides boiler sealing by preventing air ingress into the boiler via the SSC.
The cost of frequent plant downtime to replace the failed scraper idlers was further exacerbated by the regular purchase of new units. SKF’s success with a similar application and design prompted the customer to turn to the bearing and rotating specialist for an efficient and sustainable solution.
SKF proposed the supply of sealed SRBs (Spherical Roller Bearings), a quality reconditioning procedure on the scraper idlers and an overall redesign of the internal sealing arrangement. SKF’s Senior Application Engineer, Cody Petersen, explains that the highly contaminated operating conditions merited the utilisation of sealed bearings. “These bearings eliminate the possibility of contaminant ingress, thus increasing overall bearing life expectancy, equipment availability and subsequently application running time.” SKF supplied 28 units, each unit comprising two bearings, thus giving a total of 56 bearings.
“We proposed a complete redesign of the internal sealing arrangement due to the fact that the existing units were only lasting for approximately six months after installation before either getting stuck i.e. guide wheel seizure or leaking prematurely,” continues Petersen.
The SKF team carried out a redesign of the entire internal geometry, shaft, hub and guide wheel. “We also manufactured custom seal cartridges to house custom seals manufactured by SKF locally and we partnered with an accredited SKF supplier to recondition the housings.”
“Our solution has created tremendous value for our customer on several levels. In addition to a significant decrease in plant downtime, the prevention of water/ash slurry leakage has, most importantly, resulted in a safer working environment. Alongside cost savings, the reconditioning and reuse of the housings also saved the customer on time due to a faster overall turnaround time while lowering CO² emissions, ultimately benefiting the environment.”
Since the installation of the first units, SKF has received a great deal of positive feedback from the customer who has continued placing further orders for reconditioned units. “We have established an excellent working relationship with our valued customer, and we are continually implementing improvements on the current design to deliver the most optimal solution,” concludes Petersen.