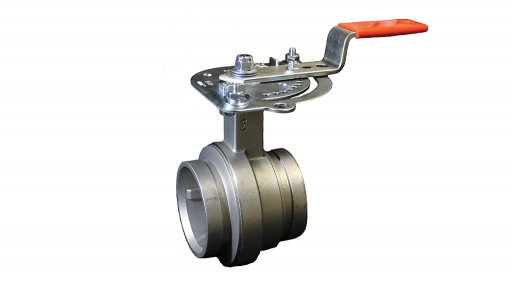
461 SERIES BUTTERFLY VALVE The valve is available in 50 mm to 200 mm nominal bore sizes, with a variety of operating options, including lever handle and gear
Mechanical pipe-joining systems manufacturer Victaulic launched its grooved-end 461 series butterfly valve in South Africa this quarter, expanding on the company’s Vic-300 MasterSeal butterfly valve line to include stainless-steel-body variants.
“The 461 series fits seamlessly into the existing line of Victaulic butterfly valves, which are manu- factured in the US, and we are pleased to offer our customers in South Africa a reliable, cost- effective and efficient solution for heating, ventilation and air conditioning, as well as potable water and industrial system applications. The stainless steel valve provides the same level of reliability the industry has come to expect from Victaulic and is ideal for any application where corrosion is a concern,” says Victaulic Africa regional manager Barry van Jaarsveld.
The 461 series valves feature a patented seat design, which assures 360º sealing. The pressure- enhanced seat compresses to form a larger seating area as the pressure increases. The seat design also contributes to the low breakaway torque capabilities of the MasterSeal valve.
This design enables the 461 series butterfly valve to handle pressures of up to 2 065 kPa and for bidirectional dead-end services at full working pressure.
The valves are available in 50 mm to 200 mm nominal bore sizes, with a variety of operating options, including lever handle and gear. They are standards and certification organisation NSF International-certified in accordance with ANSI/NSF 61 for cold 23 °C and hot 82 °C potable water service and ANSI/NSF 372.
About Victaulic
The company has been a global leader in the production of grooved mechanical couplings and pipe-joining systems since 1919. Used in the most demanding markets, Victaulic’s innovative piping technologies and services limit downtime while increasing safety, ensuring reliability and improving efficiency. The company has 15 major manufacturing facilities and 28 branches worldwide, employing more than 3 600 people, with 43 languages spoken among them.
With more than 900 active global patents, Victaulic solutions are being used in 115 countries across diverse business lines, including oil and gas, chemical, mining, power generation, water and wastewater treatment, military and marine, as well as commercial building and fire protection.
Victaulic mechanical pipe-joining systems are used in projects as diverse as coal producer Glencore’s Boschman colliery, in Mpumalanga, and the water bypass pipeline in Springbok, in the Northern Cape.
Providing sustainable solutions, Victaulic is a member of the Green Building Council of South Africa and building environment assessment and rating organisation the Building Research Establishment Environmental Assessment Methodology.