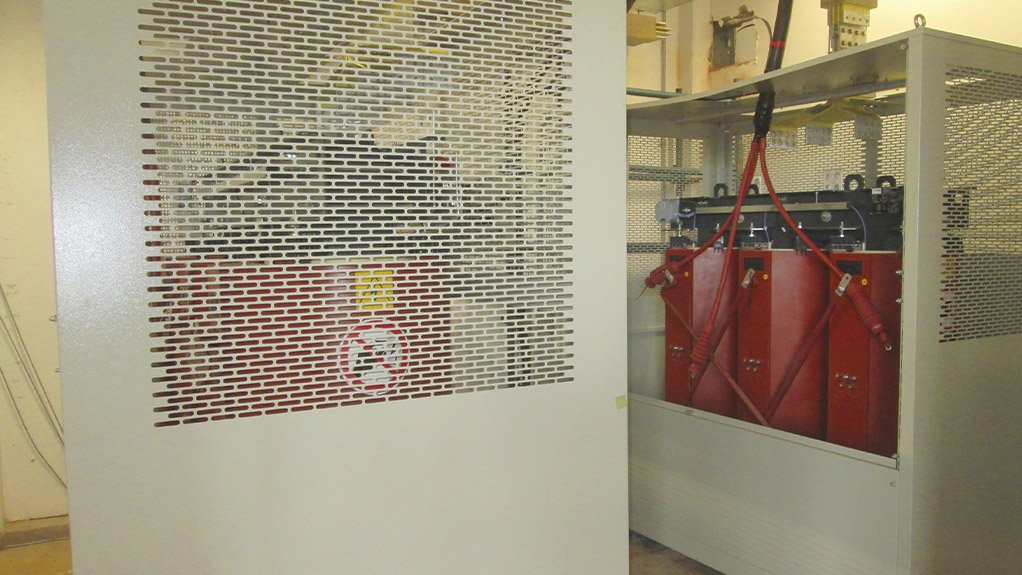
Dry-type transformer specialist Trafo Power Solutions has delivered transformers and other electrical upgrades for a global beer maker’s expanded facility in Gauteng. In addition to supplying three transformers, the company interfaced closely with the customer’s Europe-based engineering team as well as with local electrical contractors and consultants.
In addition to the supply of three transformers, the customer was also looking for a partner who would interface with the suppliers of various aspects of electrical equipment, according to Trafo Power Solutions managing director David Claassen.
Trafo has therefore interacted closely with the customer’s Europe-based engineering team on the one hand, and with local electrical contractors on the other.
Meeting high-pressure deadlines, three transformers were designed, supplied and commissioned. These included a 1250 kVA and a 1600 kVA unit – both with 11kV to 400 V capacity – as well as a 2000 kVA unit for 11 kV to 690 V application.
“These transformers all comply with the European Directive on Efficiency and are the lowest-loss dry-type transformers available,” Claassen says. “This was the customer’s specification, as they place strong priority on energy efficiency worldwide.”
Also, in the scope of work was medium voltage switchgear, including two ring-main units (RMUs) with one a three-way and the other a four-way.
“We modified the RMU’s in line with the customer’s requirement, including a battery-tripping unit (BTU) on each,” he says. “This ensures there is power available regardless of the condition of the circuit breaker.”
As a brownfield project, there was considerable adaptation of design to suit the plant configuration. Instrumentation was located on a raised base, for instance, where voltage transformers and current transformers were installed for monitoring each RMU.
“We also supplied three very specialised distribution boards (DBs) between the low voltage transformers and the new sections of the plant and new brewhouse,” he says. “This non-standard design has a modular type assembly conforming to EIC 61439 and EIC 61641.”
This provides the highest level of safety and can be supplied by only a few manufacturers in South Africa. The DBs, which are fully-tested for IEC 61641 (Internal Arc Fault), incorporate 2500 Amp incomers, distributing through various feeder circuits to the rest of the plant. Two of the DBs are 400 V and the third is 690 V.
“Another non-standard aspect of the DB supply was its Form 4A design, so that each compartment is separate,” Claassen says.
He highlighted the company’s in-house capacity to provide complete solutions within tight deadlines. In this case, the design, manufacture, delivery and commissioning were achieved in just three months. Installation was also co-ordinated with plant shutdown schedules to avoid costly downtime.
“We develop non-standard solutions where these are required, and take responsibility for integration, compatibility, quality and timeframes,” he says.