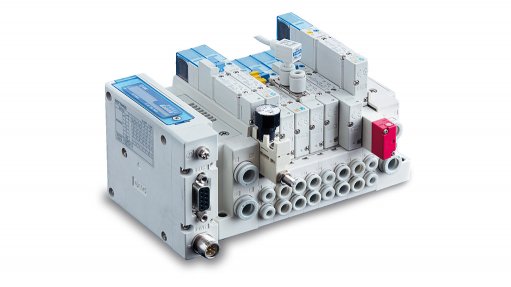
SMC Pneumatics South Africa, a leading provider of pneumatics, continues to drive design excellence and application with its SY series of Valve Manifolds which is manufactured locally at its production facilities in Midrand, Johannesburg.
New-generation benefits
The unique, all-purpose series of Valve Manifolds from SMC Pneumatics is available in three sizes, namely: SY3000, SY5000 and SY7000. Thanks to its flexibility and innovative redesign, the SY series sees a 29% space saving in installation while offering increased flow rates.
Looking at the SY series’ use, two of the smaller valve sizes or two larger valve sizes can be mixed on one manifold to closely match application flow requirements. The manifold offers piping options to the top, side or bottom with various port size options – this results in a flow rate of up to 1500 litres per minute (LMP) through the biggest valve mounted on the manifold.
With the food and beverage industry in mind and adhering to its stringent standards, the SY5000 series also includes a new IP69K manifold which is suitable for wet areas and can withstand wash down and cleaning.
Ernst Smith, SMC Pneumatics Product Manager explains: “The SY series has taken the market by storm and today many of our customers are benefiting from its flexibility and local assembly here in Johannesburg for shorter lead times”.
“The SY series offers further savings due to its ability to drive bigger cylinders with reduced cycle times, mitigating the need for larger, more expensive solenoid valves”. The SY series is available in either rubber or unique metal seal versions with the latter optimized for higher operating frequencies and extended lifetime performance; boasting switching cycles of up to 200 million cycles.
The SY series incorporates SMC’s energy-efficient V100 pilot valve, a power saving option that reduces consumption (per valve coil) down to just 0, 1 Watt.
Flexible innovation and customisation
SMC’s SY series offers a myriad of options, optimised for customised projects and applications. Here are a few examples:
- A single valve can be mounted on a base which will offer flow rates exceeding 1500 LPM - connected with SMC’s M12 waterproof connector;
- The valve can be supplied fitted with a residual pressure release valve that enables manual dumping of residual compressed air in the cylinder;
- Power and control options such as: D-sub connectors; flat ribbon cables; terminal block box; pre-assembled leads; and circular connectors, offering options for serial transmission;
- Applicable Fieldbus protocols include PROFINET, PROFIBUS, DeviceNet, CC-Link, EtherNet/IP, EtherCAT, CANopen, AS-Interface, OMRON CompoBus/S and CompoNet. Digital as well as analogue inputs and outputs can be added to suit customer application requirements.
Safety remains key
“Safety is always considered when we look at products and customer applications,” adds Smith.
Overall safety in applications has been improved via optional configurations:
• The addition of a built-in back pressure check, it can also be retro-fitted afterwards;
• The addition of a manual pressure release valve for every cylinder where required;
• A supply shut-off spacer per valve to allow the maintenance team access to the system or part thereof while the rest of the manifold is still pressurised;
• Spacers with double check valves in working lines to enable intermediate stops or for drop prevention of loads in vertical applications; and
• Slide locking manual override function with double action and long distance visual indication.
In-house production facilities
SMC’s state-of-the-art production facilities in Midrand focuses on cylinder production, manifold assemblies and air preparation combination sets. “Our in-house production facilities have been well received by the market. We are now able to configure and assemble manifolds to exact requirements in a matter of hours. Benefits have been experienced in cases such as breakdowns and for those wanting larger manifolds matched to unique requirements in a hurry.” concludes Smith.
Delivery of these items will take place on a three-tiered basis:
- Regular orders within three days
- Larger orders within two weeks
- Breakdowns with a same day service
The new trend in automation for flexibility and products that are lighter and more compact is on the rise, and according to SMC, they anticipate this type of product development becoming more and more standard.