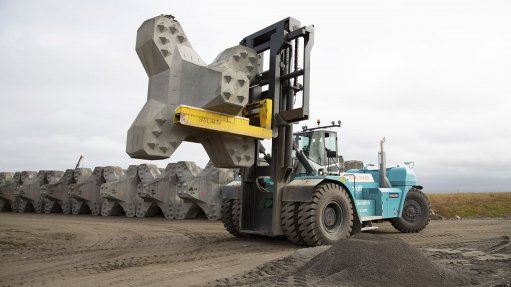
There is often a misconception that a tailor-made machine designed and built to fit specific job requirements will be more expensive than a standard, unmodified machine.
On the face of it, a standard machine might seem cheaper, but that may only be so when you compare the purchase price of both machines.
To make a valid comparison, one must look at the bigger picture and take into consideration the savings that can be realised from a purpose-built machine, which can cut down work time considerably and do the job more efficiently than a standard machine.
Tailor-made machines, also known as custom or bespoke machines, offer several benefits for various industries and applications.
In the case of heavy lifting machines, adaptations to the standard machine can provide advantages such as perfectly fitting the intended application, ensuring optimal performance and efficiency.
Lenny Naidoo, Acting National Operations Manager at CFAO Equipment SA’s Heavy Lift division, which sells big forklifts to container handlers and the ports industry, says custom machines can be engineered to streamline processes, leading to higher productivity and reduced downtime.
“While the initial investment for custom machines can be higher, they often lead to long-term cost savings by improving efficiency and reducing operational costs. Tailor-made machines can be designed to meet changes in production requirements or new processes, making them adaptable to evolving needs,” says Naidoo.
Most often the request for a tailor-made machine comes from the customer who needs more than what a standard machine offers. Konecranes tailor-made a tyre handler to be used in the mining industry in Chile, Australia and South Africa. Strong and agile, the tyre handler is designed to carry extremely heavy wheels that cannot be lifted even by a few men.
The Heavy Lift division received a request for a specialised piece of equipment which came from a company that worked with long, heavy pipes. A Konecranes heavy lifting forklift was modified with the addition of a special pipe handling attachment to move the pipes around.
Naidoo says it is important for customers to use solutions that are tailored for the elements of specific products and processes, as this will contribute to greater efficiencies and cost effectiveness.
“A custom-made machine can provide better solutions and quicker turn-around time, which is why we welcome customers who discuss their needs with us when they have a special operation that cannot be easily serviced by a standard machine,” says Naidoo.
Naidoo also cites the case of a customer who wanted a machine to lift very heavy concrete slabs, weighing 55 tons each. Konecranes built a tailor-made 60-ton machine with a 1,5-metre load centre. A load centre on a forklift is the distance from the face of the forks to the load’s centre of gravity. A standard machine has a 1,2-metre load centre, but in this case, it was extended to cater for the heavy cargo.
“If it happens that we get multiple customer requests for the same specialised equipment, the tailor-made machine will then form part of the standard Konecranes range. It becomes easier to manufacture because the research and development, as well as the tooling, has already been done. The 60-ton forklift with the 1,5-metre load centre is now offered by Konecranes as a standard unit,” Naidoo says.
He adds that using tailor-made machines has the advantage of providing a competitive edge to customers by allowing for unique processes or product offerings that are not available in off-the-shelf solutions.