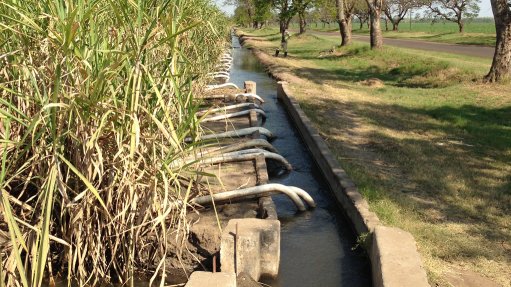
SWEET SCIENCE
WSP completed a water use quantification project for a major sugar producer in May
Photo by: Orange Ink
Multidisciplinary engineering and design consulting firm WSP Africa’s environment and energy business unit completed a water use quantification project in May, which assessed the use and management of water at each of the agricultural and industrial operations of a major producer in the Southern Africa sugar industry.
The project, which started in November last year, monitored the quality and quantity of water being consumed across 13 sites – including mills, refineries and distilleries – at various locations, situated in KwaZulu-Natal, Swaziland, Zambia, Malawi, Mozambique and Tanzania.
“The sugar industry is a major stakeholder in the agricultural industry in sub-Saharan Africa and more locally in KwaZulu-Natal. Historically, this coastal region was always known for its reliable rainfall patterns, which made the region well suited to farming sugar as – from crop cultivation to steam production in the milling process – the sugar industry relies heavily on water. However, the quantity and quality of available water resources are becoming more strained,” says WSP environment and energy Africa MD Carl Haycock.
WSP environment and energy principal consultant Helen Hulett tells Engineering News the sugar industry company required quantification of its “water footprint, as well as the quality of water discharge and its impact on the environment”.
“When looking at the client’s agricultural operations, we set up models to monitor and report on where each site gets its water from, the amount of water being consumed at each site and what the water is being used for, as well as if there are any potential losses or gains – that if addressed appropriately may be turned into economic opportunities or potential cost savings.”
She notes that the model measured and reported on the irrigation systems and the effects of surface water and precipitation.
“An industrial water and wastewater specialist was appointed to investigate the client’s sugar mills and distilleries, and develop a water consumption model,” Hulett recounts, adding that 11 milling and two distillery operations formed part of the project.
The water consumption models enabled WSP to investigate methods to improve reuse- recycling efficiencies within the milling operations.
“We developed a programme that enabled the client to update the system on a monthly basis and produce water footprints for all its operations going forward. “The system also identifies an efficiency matrix, highlighting risks and opportunities pertaining to water consumption and use,” Hulett highlights.
She explains that the catchment supplying each of the operations is unique and, therefore, each catchment required its own risk map to determine each operation’s level of risk.
“The focus of the project was to determine the effects climate change is going to have on the client’s agricultural and industrial operations. The impacts of decreasing rainfall during the dry season, prolonged dry seasons and the increasing intensity of flood and drought events on the client’s agricultural operations, were all investigated,” Hulett says.
She notes that the factories and agricultural operations investigated in KwaZulu-Natal were significantly more water efficient than those of the other regions participating in the study, owing to South Africa’s strict regulatory and cost drivers.
“There are huge water efficiency and water use opportunities in the rest of Africa, as regulation and costs have not been pushed as strongly. Systems that monitor and quantify water use need to be put in place, as efficiency is usually developed from using these systems that, in turn, can be used to facilitate improved water use,” Hulett states.
Haycock concludes that determining an operation’s water footprint may trigger other operational efficiencies, as the system can identify energy inefficiencies in, for example, pump systems. This will enable companies to quickly identify and manage such inefficiencies and, therefore, improve energy consumption and reduce operational costs.