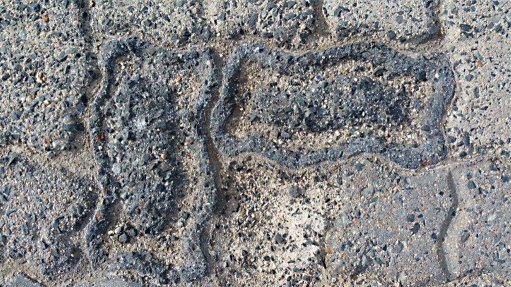
Although concrete is an extremely robust and forgiving construction material, with almost all concrete placed outlasting its designed service life, some durability issues do crop up and can be overlooked. John Roxburgh, lecturer at The Concrete Institute’s School of Concrete Technology, outlines some of the less common durability issues that may be encountered in concrete practice.
The corrosion of steel within the concrete is the most prevalent durability problem associated with concrete. For this reason, great care is usually taken to ensure that the correct reinforcing steel is placed in the correct position with enough concrete cover to it. However, what is sometimes overlooked is the environment into which the concrete is placed – a factor that could substantially negatively affect the planned durability targets.
Listed below are a few of the better-known mechanisms that could lead to deterioration of concrete. Durability issues, generally, can be categorised under two main headings: mechanical (and physical) deterioration, and chemical deterioration. Chemical deterioration, furthermore, can be subdivided into the chemical dissolution of the hydration products and the chemical conversion of the hydration products.
Mechanical (and physical) deterioration mechanisms:
Erosion and Abrasion: Erosion is caused by fluids, most often water, containing abrasive particles wearing down the surface of the concrete. Abrasion is caused by wheeled traffic on floors and pavements as well as abrasive material, as in ore passes and silos, wearing down the surface of the concrete. Strong concrete with little surface laitance, well cured and finished off along with abrasive resistant large aggregate will slow down the rate at which the concrete surface will wear. Specialist surface hardeners will also help reduce wear.
Cavitation: The collapse of very high pressure vapour bubbles, created by fluid jumping off the surface of the concrete due to sudden changes in direction of the fluid, can lead to massive damage to the concrete within a short period of time. Aerating the fluid - such as often done on dam spillways - to prevent pressure build-up is an effective way of preventing cavitation.
Salt crystallisation: This is often called “salt jacking” and tends to occur along the coast where the concrete is subject to high concentrations of salt. Salt in solution is transported into the concrete and, when the concrete dries out, it re-crystallises with the resulting expanding salt crystal exfoliating the surface of the concrete.
Freeze-thaw: Ingress of water into the concrete that subsequently freezes can cause the formation of cracks due to the expansion of the ice. Air entrainment can effectively prevent this. The size of the air bubbles and, more importantly, the spacing of the bubbles are key factors in how effective the air entrainment will be.
Chemical deterioration mechanism:
Dissolution of hydration products:
Acid attack: The calcium in the concrete hydrates have a high solubility in acids. Often a sacrificial calcareous aggregate is used to get an even wear and slower disintegration of the concrete surface. With strong acids, a sacrificial layer or an acid resistant coating is more effective in protecting the concrete.
Soft or pure water attack: Waters with very low ion contents will cause the dissolution of the hydrates within concrete. Soft or pure waters are often found in waters that have not come into contact with calcareous rock.
Chemical conversion of hydration products:
Alkali Silica Reaction (ASR): Reactive silica’s contained in the aggregate can react with active alkalis within the concrete pore structure. This forms an expansive gel that results in the concrete cracking. Avoiding aggregates containing reactive silica, minimising the active alkalis within the concrete, and preventing the ingress of water into the concrete are effective measures in preventing ASR.
Sulphate attack: A combination of sulphates, calcium hydroxide and tricalcium aluminates in the concrete can lead to the formation of two expansive compounds: gypsum and ettringite. This can cause the concrete to soften and crack. Using sulphate resisting cement or extending the cement with fly ash or slag can help prevent sulphate attack on the concrete. Also ensuring the sulphate content in the aggregate and mixing water is kept low and preventing the ingress of water into the hardened concrete will prevent sulphate attack.
Interestingly, all of the above described deterioration mechanisms can be mitigated or even prevented by designing the concrete mix with a lower water to cement ratio and implementing good site practice by ensuring excellent compaction and optimising curing. By doing this, the concrete will be less permeable which is key to a more durable concrete.
Although the mechanisms mentioned above are by no means exhaustive with regards to concrete’s durability, they serve to illustrate the wide spectrum of environments that concrete may be subjected to. There are many well researched methods of ensuring that concrete will perform for its service life within any specific environment it is place, however it is important that engineers and concrete practitioners should take heed of these environments or potential durability problems.
Further information: John Roxburgh, tel 011 315 0300 or visit www.theconcreteinstitute.org.za