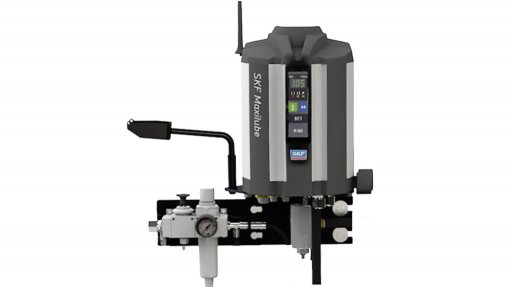
SKF enhanced personnel safety, increased machine reliability, boosted uptime and delivered substantial time and cost savings for a leading paper mill in Morocco with the installation of a complete Maxilube lubrication system on a paper machine.
The customer had little control over the lubrication of bearings on one of their paper machines. Extremely restricted safety procedures prohibit any approach to the running machine. The customer’s only solution therefore was to grease the bearings in the wet end when the machine was standing still during programmed stoppages. As lubrication could only be performed on the bearings every 35 to 60 days, lubrication was insufficient when the machine’s running time increased, causing bearings to overheat and ultimately fail prematurely.
The customer subsequently requested SKF to supply and install a lubrication system on the wet end of the paper machine. Following numerous meetings and discussions with the SKF Morocco team, the customer chose the Maxilube monitored dual line solution. As the installation had to take place during planned machine downtime when all maintenance operations were carried out, SKF only had a five-day window period in which to install the entire lubrication system and was the only supplier who was willing to accept this tight deadline.
When the customer postponed the project for approximately four years, SKF faced new challenges. The customer contacted SKF in August 2023, requesting that the team again commence work on the lubrication solution. The complete lubrication system had to be installed before the end of October 2023 to take advantage of the scheduled five-day machine shutdown. Challenge accepted!
Thanks to the support from SKF’s Muurame factory as well as the efforts of all the commercial colleagues at the Customer Service, SKF managed to get the equipment three days prior to the start of the customer’s technical shutdown, which greatly assisted the team with the necessary preparation work.
The monitored Maxilube lubrication system is connected to a dualset unit with two MPB pumps for automatic drum change when one of the drums is empty. The lubrication solution also includes SGA distributors with cycle and alarm sensors installed on the distributors to monitor the efficiency of lubrication operations. All components are manufactured from AISI316 stainless steel to ensure lasting reliability. The flexible system has the potential to connect alarms to the customer’s DCS going forward.
The SKF team completed the project within ten days - from equipment delivery, assembly and testing to final commissioning and hand over; this included five days of downtime during machine shutdown.
According to the customer, SKF achieved the best score amongst all the other projects that were running on the machine at the same time. Extremely satisfied with the SKF Morocco team’s efficiency and professionalism, the customer immediately requested a proposal from SKF for a Flowline oil recirculation system for 110 bearings to potentially replace an existing system.