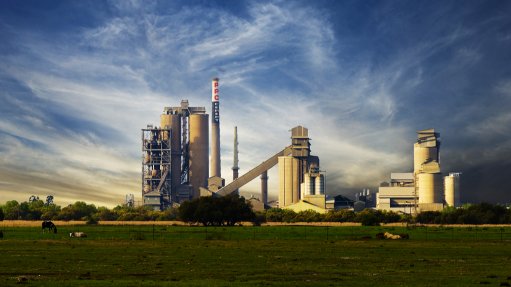
PPC SLURRY Production at PPC’s Slurry cement manufacturing operation in the North West is set to increase to 1.9-million tons a year following the completion of the SK 9 kiln
JSE-listed cement producer PPC last month invited media to a tour of its Slurry operation, in the North West, and the construction site of the R1.7-billion Slurry Kiln (SK) 9 project, which is scheduled for first clinker production at the beginning of next year.
The brownfield project, which started construction in October 2015, will increase cement production at Slurry from 1.2-million tons a year to 1.9-million tons a year, following first clinker production.
PPC CEO Darryll Castle told Engineering News during the site visit that the SK 9 project would replace outdated and inefficient kilns at Slurry and would ultimately result in the operation becoming more competitive. Further, the increased production at Slurry would help PPC “attack the areas of South Africa that really make sense to deliver from Slurry”.
Further, Castle noted that cement demand in South Africa was predicted to increase in the near future and the increased production capacity at Slurry would help PPC take full advantage of the growing market.
“[This project] is about us being dominant, being the market leader and making sure we get the next part of the expansion in the South African environment,” he stated.
Meanwhile, PPC projects executive Leon du Plessis explained that SK 9 would replace the outdated SK 5 and 6 units, which would be demo lished, as well as the soon-to-be-mothballed SK 7 unit.
The SK 5 and 6 units started production in 1959 and 1961 respectively, while SK 7 started production in 1968.
He pointed out that SK 9 would also comply with National Environmental Management Air Quality Act requirements, which will come into effect in 2020. The Act requires that dust be limited to 30 mg/Nm3 of air across a site.
Another component of the SK 9 project will involve the replacement of the SK 8 unit’s electrostatic precipitator with a bag filter to ensure compliance with the Act’s requirements. SK 8 is expected to be recommissioned late next year.
Du Plessis highlighted that, while construction of the new kiln was unexpectedly delayed, the contractor, CBMI Construction, a subsidiary of Chinese company Sinoma, was able to progress the project sufficiently to still meet the 25-month project delivery schedule.
Modern Kiln Design
PPC senior projects manager Dipeen Dama explained that the SK 9 unit would incorporate the latest technologies and energy efficient systems, in line with global industry best practices.
One of the most significant technologies used in SK 9 is its six-stage preheater with an in-line calciner, which Dama pointed out helps improve the thermal efficiency of clinker production. Further, SK 9 will boast a multichannel burner, allowing for flame-shape adjustment, thereby providing the “optimal heat transfer, which is important for the chemical reactions that take place within the kiln line”.
He highlighted that the new kiln would also employ the latest-generation “walking floor” grate-type cooler technology, which significantly increases the heat recovery of the kiln.
Dama asserted that up to 74% of the heat would be recovered, which would then be used in other processes in the plant, thereby significantly reducing the electricity needs of SK 9.