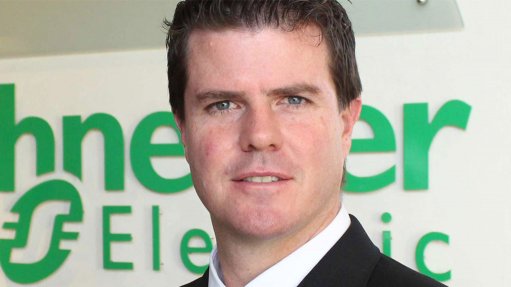
In an ever-changing digital world, for everything from new business models and new consumer technologies to new infrastructure, energy and power systems – the digital transformation is inescapable. The fourth industrial revolution, or smart manufacturing, has accelerated the move to digital technologies that offer a competitive advantage to every company and every geographical zone that adopts them.
Augmented reality, IoT, IIoT, machine learning and predictive maintenance are making companies more efficient and innovative, boosting their competitive advantage. Schneider Electric, the global leader in the digital transformation of energy management and automation, recently took to Hannover Messe 2018, the world’s leading trade show or industrial technology, in Germany to showcase its latest innovations for industrial companies.
As energy and automation develop into a more digitally connected environment, these new technologies are capable of ensuring that power-sensitive automation equipment remains operational, boosting power reliability and cost savings by improving the speed and accuracy of the processes they are tasked with.
Bridging the divide between complexity and human capabilities by using control devices and technology for automated operation and control, digitisation allows for better support and faster decision making by providing operational insight, encouraging efficient use of resources to maximise assets and production output, simplifying tasks, and integrating the implementation of plant strategies.
“At Schneider Electric, we believe that integrating power and automation systems through IoT has the potential to bring together the best features of both systems, enhancing processes while introducing safer, more reliable, efficient, sustainable, and connected power,” Marc Ramsay, Vice President for the Industry Business Unit, Schneider Electric South Africa.
As the leader in powering and digitising industry, Schneider Electric is uniquely positioned to drive the digital transformation of today’s growing industrial automation markets and assist industrial customers in their conversions. Significant changes are fundamentally accelerating this movement in the industrial space.
“With EcoStruxure for Industry, Schneider Electric offers a truly unified engineering approach that can be deployed across multiple industrial segments. Leveraging our unique partnership with AVEVA, we can offer an unmatched set of solutions covering all aspects of digital asset management from process simulation to design, construction and manufacturing operations management and optimisation,” Ramsay said.
Schneider Electric’s EcoStruxure for Industry offers open, interoperable, IoT-enabled system architecture and platform, where users benefit from enhanced value around safety, reliability, efficiency, sustainability, and connectivity.
Leveraging all advancements in IoT, including mobility, sensing, cloud, analytics, and cyber security through connected products - Edge Control, Apps, Analytics and Services, EcoStruxure has been deployed in over 480,000 sites worldwide.
“With the support of 20,000 system integrators and developers, EcoStruxure currently has 1.6 million assets under management, and that figure is expected to grow by 25% year-on-year for the foreseeable future. This figure ties in with Accenture’s recent report, citing that at present, 64% of executives believe that a failure to leverage digital will cause their companies to struggle for survival,” says Marc Ramsay, Vice President for the Industry Business Unit, Schneider Electric South Africa.
Strengthening their commitment to digitising industry, Schneider Electric also unveiled EcoStruxure Machine Advisor during a presentation at Hannover Messe, 2018.
EcoStruxure Machine Advisor now make it possible to track, monitor and fix machines in the field while reducing support costs by 30 to 50%.
“Where managers struggle to track the history of the many machines that fall under their scope of responsibility, or when parts need replacing, production is interrupted, and the downtimes are much too long. Maintenance technicians often spend far too much time attempting to locate different sets of documentation before they can begin productive work on fixing the machine. Schneider Electric’s recent breakthrough with this new technology is now directly addressing these challenges by providing new ways of both gathering, centralising and displaying machine-generated data.”