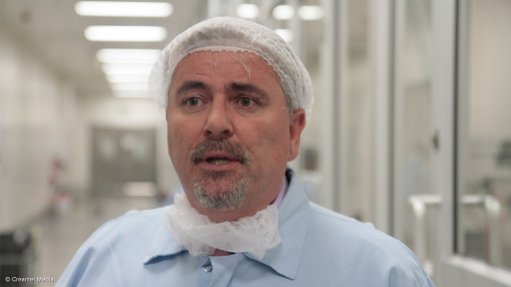
John Fagan
Photo by: Duane Daws
Bucking a global trend that has seen a number of pharmaceutical firms withdrawing their manufacturing capabilities from emerging countries, Sanofi South Africa told journalists on Thursday that the group was “serious” about maintaining its production facilities in developing markets, citing a recent €3-million investment to expand the manufacturing capacity for tuberculosis (TB) and HIV/Aids medicines at its Tshwane-based site.
This expansion project enabled the company – an offshoot of the world’s fourth-largest pharmaceutical group Sanofi – to increase its production capacity of these drugs to 350-million tablets and capsules, or 10-million TB packs a year, servicing around one-million South African patients.
The expansion came as the company was awarded 95% of a government tender to provide TB medication to public healthcare institutions, making it the largest government supplier of these drugs.
“Around 70% of the products we manufacture at this facility are destined for South Africa’s public healthcare system, with the balance exported to emerging markets, such as Russia, Mozambique, Argentina and Thailand,” commented Sanofi South Africa GM John Fagan.
Meanwhile, after boosting its Aids treatment ambitions by signing a partnership agreement with global research-based pharmaceutical company Hetero for the development of an antiretroviral (ARV) product portfolio in 2012, the Waltloo-based facility now also manufactured 12-million ARV drug packs a year.
Sanofi South Africa said the agreement had enabled it to deliver quality ARV products at affordable prices and to increase the manufacturing benefit of these medications in South Africa, as they were locally produced.
“For example, [our] ARV drug Tenofovir Winthrop retails at less that $0.10 a day, while our fixed-dose combination TB drugs Rifafour and Rifinah cost $0.07 a day,” he outlined.
DEVELOPING MARKET FOCUS
Elaborating on the group’s strategy to retain a presence in emerging markets, Fagan said sales into these regions represented almost a third of the global group’s sales, bringing in revenue of some €11.1-billion a year.
“It’s easy to do business in the developed world, such as Europe, but we also want to be in emerging markets, as most of the global population lives in these regions and they have very different [pharmaceutical] needs [to] those living in developed economies,” he explained, adding that the company currently had seven manufacturing facilities in Africa.
He further described the local subsidiary as a “big player” in the development of vaccines, noting that it was engaged with government in building up South Africa’s local vaccine capacity and was implementing the technical transfer of knowledge related to direct-to-pharmacy hexavalent vaccines to treat polio and hepatitis B.
“[As a group], we spend about R40-billion a year on research and development after identifying gaps in the global pharmaceutical industry. We currently have 50 vaccines under clinical development, which will likely come to fruition within the next four years,” Fagan noted.
The multinational also had an established counterfeit product detection and analysis centre in Paris, France, at which some 20 000 “suspicious” pharmaceutical products had, thus far, been tested, with some 30% proving to be counterfeit.
Many of these originated in African markets.