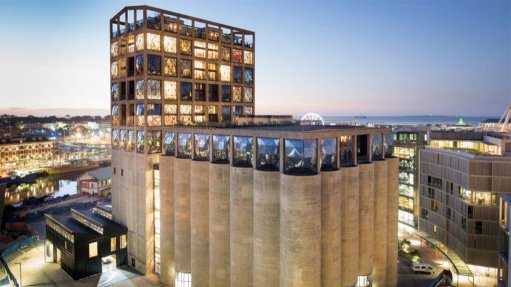
Aesthetically-pleasing architectural shapes are particularly difficult to cast. This requires a close collaboration between the formwork supplier, architect, engineer, and contractor in terms of devising the most optimal and cost-effective engineering solution.
The main challenge with difficult architectural shapes is not only how to form them quickly and cost-effectively, but also how to maintain the necessary consistency during construction, PERI South Africa Technical Manager Riaan Brits and Senior Project Engineer Andrew Rowe explain. It is for this reason that PERI has developed innovative solutions such as RUNDFLEX, its flagship product for circular and curved formwork.
RUNDFLEX consists of pre-assembled standard panels for curved walls that can be adjusted to suit the required radius, with no modification work on the panel. Further advantages include less installation effort due to the pre-assembled units.
Adjustment is quick and easy by means of a template and spindles with self-cleaning hexagonal threads. In addition, the flexible adjustment of wall internal radii of 1 m and larger means that RUNDLFEX is a highly variable solution for a range of architectural requirements and features.
The pre-assembled panels allow for a maximum permissible fresh concrete pressure of 60 kN/m². Six panel heights are available (0.60 m, 1.20 m, 1.80 m, 2.40 m, 3.00 m, and 3.60 m) and three panel widths (external: 2.50 m, 1.28 m, and 0.85 m).
Panel connections and compensations up to 10 cm are possible with the BFD alignment coupler. Other features are-determined tie points, horizontal extensions up to 7.80 m panel heights, and the availability of components for working and concreting scaffolding, as well as for providing support.
WBHO Construction selected RUNDFLEX when it was appointed in 2015 to transform the derelict Silo Building at the Victoria & Alfred Waterfront in Cape Town into the Zeitz Museum of Contemporary Art Africa.
Here the main construction challenge for the formwork supplier was the fact that the existing silos had to be resleeved with a 350-mm-thick concrete layer, to a very small radius of under 2.5 m, with an average silo height of 33 m. The concrete sleeving also had to incorporate various splays.
RUNDFLEX was ideal for the continuous adjustment of the tight inner radii needed as the silo resleeving progressed vertically. This had to be carried out in conjunction with an integrated PERI BR platform system to allow for the safe installation of the RUNDFLEX panels by crane. Each silo was built up in 2.5 m high vertical forming sections.
The day after each circular wall section was cast, the RUNDFLEX system was removed from the silo in question, and placed on a cleaning deck, where the formwork was cleaned and serviced prior to it being deployed again.