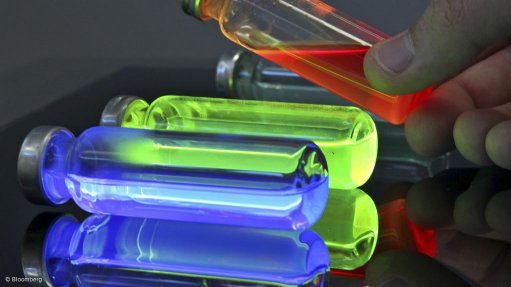
SAFETY ABOVE ALL
Ishecon’s training helps engineers to build and operate safe chemical plant installations
Photo by: Bloomberg
Major Hazard Installation (MHI) regulations for hazardous chemicals and petrochemicals industries – which fall under the Occupational Health and Safety Act (OHSA) – are under review to align them with international standards.
Risk assessment service provider Ishecon founding member Nigel Coni tells Engineering News that the revised MHI regulations are scheduled to be announced next year.
The original MHI regulations were drawn up before 2000, but have been under review since 2008.
“There is a problem in deciding when a chemical installation becomes a hazardous chemical installation. International practice is to list the chemicals that a company handles, and if it exceeds a certain threshold quantity, then the installation is classified as an MHI and requires a quantified risk assessment.”
Ishecon is part of a technical committee appointed by the Department of Labour to propose MHI regulatory changes.
“The regulations changes will conform to European standards of MHI and will provide clearer guidelines for risk assessment requirements for companies,” notes Coni.
Risk Assessment Process
Ishecon has provided chemical process safety consulting services to the chemicals industry since 1999.
Ishecon is an Approved Inspection Authority for MHIs – one of ten in the country. The company is assessed by the South African National Accreditation Service on a yearly basis to ensure compliance of personnel, equipment and systems used by the company.
Risks assessments entail collecting information from companies working with chemicals, assessing the chemical safety risks, and discussing findings with clients.
The process for large companies can take between three to six months, and two or three weeks for smaller companies. The OHSA requires risk assessments to be reviewed every five years.
“We help industrial clients to decide on additional risk-reduction measures, whether it is necessary to take additional risk-reduction measures and what the most cost-effective options are, as well as enable facilities to expand and create jobs while ensuring maximum safety,” says Coni.
Ishecon has done risk assessment for many petrochemicals companies in South Africa, paper manufacturers, State-owned companies’ pipeline systems, companies using large-scale cold storage refrigeration and large liquefied petroleum gas users.
The company also provides Hazard and Operability (Hazop) studies for clients, which entails analysing chemical plant designs.
“We help to make sure the engineers design chemical plant installations that are operable and safe,” notes Coni.
Safety for All
Ishecon presents three public training courses at a conference venue in Johannesburg twice yearly, usually in May and October, as well as in-house training courses on site for larger company clients.
The company presents a two-day quantified risk assessment training course for an average of ten attendees. This training helps clients to understand what the risk assessment report findings mean and interpret information for increased plant safety.
It also presents a three-day Hazop study training course for an average of 20 attendees, as well as in-house Hazop study courses for clients six times a year. The course enables clients to meet design and operation safety measures, health and environmental requirements and operability requirements.
A five-day course, Fundamentals of Process Safety Management (FPSM), is accredited by the Institution of Chemical Engineers, in the UK, and presented to an average of 25 attendees.
“This FPSM course creates awareness for chemicals companies about process safety, since smaller companies that handle, transport, store or use hazardous chemicals are often not fully aware of the safety risks and preventative measures,” Coni concludes.