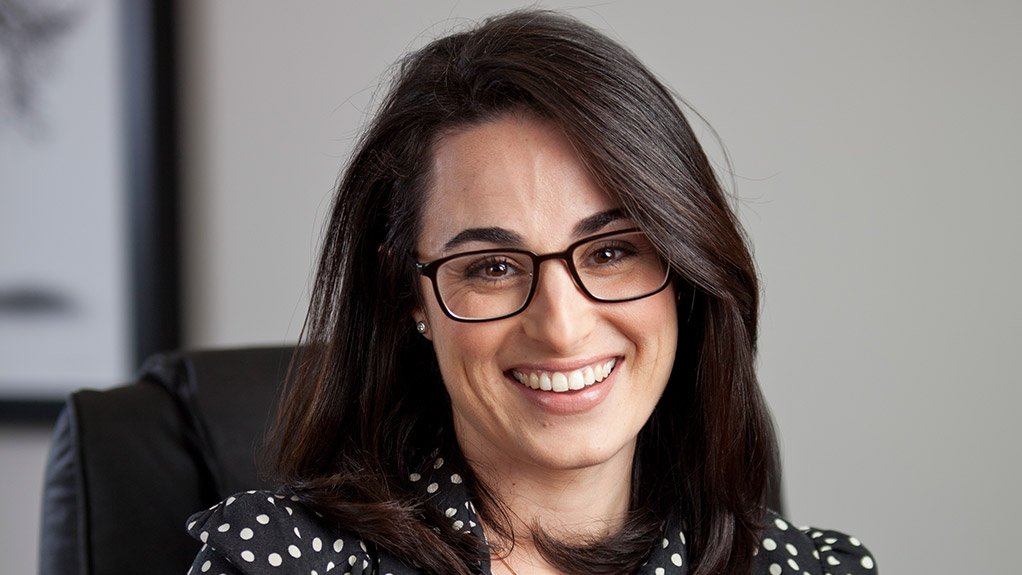
NADINE SHENKER Predictive maintenance technologies can help companies effectively extend the use of assets and improve their performance
Predictive maintenance technologies can help companies effectively extend the use of assets, improve their performance, increase their safety and prevent unplanned downtime, says business intelligence consultancy BITanium Analytics director Nadine Shenker.
Predictive maintenance is complex, owing to the necessity of a detailed understanding of the assets. For each asset, data including the maintenance history, time in operation, distance and roads travelled, age of asset and real-time readings, including speed and fuel consumption, as well as driver behaviour (if appropriate), are required to effectively predict maintenance needs.
Companies should install on-board diagnostic devices and telematics units into their most critical assets. Once sufficient data has been collected, they can build and deploy predictive maintenance models on this subset. The model can then be expanded to other assets within their fleet over time, she says.
“An early indication of failure may be something as simple as the asset using more oil than usual, which can only be determined by comparing oil use over time . . ., or the asset is vibrating more than usual or operating at reduced power.
“The most knowledgeable people from across the company must provide input to make the model robust and effective. The more information and real-time monitoring there is of an asset, the easier it becomes to predict maintenance requirements for the asset and improve operational performance,” she says.
An intelligent asset management system, such as predictive maintenance, also enables companies to reduce costs in other areas, including extending periods between scheduled maintenance and not replacing components or assets that are in good working order, despite being over a certain operating age. Understanding when an asset may fail can help prevent unplanned maintenance, highlights Shenker.
Once predictive maintenance is implemented, companies will have the ability to reduce and optimise inventory levels of spare components. This will lead to the more judicious replacement of parts, as assets are monitored more closely. Such business intelligence systems can link to enterprise systems and supply chain management systems, enabling companies to manage suppliers and costs more closely,” she emphasises.
The first step that companies can take in deploying a predictive maintenance system is to gather the correct data from assets using on-board sensors.
“After gathering the data, companies should use advanced statistical and mathe- matical techniques to derive a model that will accurately predict its maintenance requirements and manage the asset through its lifecycle. “A multidisciplinary team of business intelligence practitioners, mechanical engineers, managers and statisticians must work together to ensure the success of such a solution, ” she concludes.