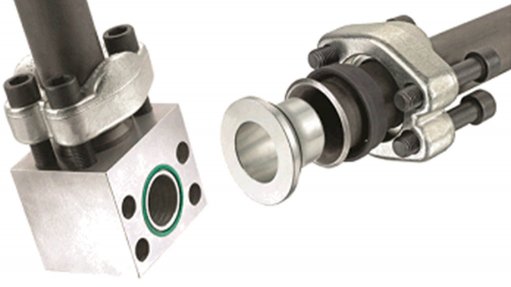
January 2017 - Parker Hannifin, the global leader in motion and control technologies, has announced that under the brand-name: Parker HPF High Performance Flange System, it is offering a mechanical flange system for machines and installations with a working pressure up to 420 bar. The product programme meets increasing requirements - especially from the press construction, injection moulding machine and mobile work unit industries.
The new flange system significantly contributes to a reduction in assembly time and costs because it dispenses with the need for error-prone and time-consuming welding processes. Furthermore, the Parker HPF system has outstanding high pressure and vibration resistance. The system performance is underpinned by DGUV certification, which has tested the use of HPF in the hydraulic equipment used on injection moulding machines as well as hydraulic and mechanical presses.
The Parker HPF High Performance Flange System is a positively locking connection system. It complements the proven product range in the area of EO-2, EO2-FORM, EO-3 and F37 connector technology, with tube outside diameters from 25 mm upwards. In industrial applications it provides the ideal replacement for welded tube connections subjected to the highest loads. The HPF system consists of a flange, an HPF insert (with O-ring recess or as a flat sealing version), a steel locking ring, and seals on both port and tube ends to ensure a gas-tight connection.
The system is suitable for use on steel tubes from size 25 mm up to 150 mm with tube wall thicknesses up to 20 mm. The associated steel components are supplied with environmentally friendly and extremely corrosion-resistant Cr(VI)-free surfaces.
Flange sizes range from ¾” to 5” and are available in accordance with ISO 6162-1, ISO 6162-2 and ISO 6164 standards. Tube flaring is effected in a tulip shape and has no sharp edges. Uniform loading of the surfaces in the whole flange area is achieved with this technology, resulting in very high break resistance.
The forming process is carried out utilising Parflare machinery specially developed for these products and providing hydraulic axial compression. Almost all tube sizes can be machined with just three flaring pins. Even large-format tubes can be simply, and above all quickly, handled, thanks to the integrated tube stop, exemplary ergonomic design and the high operating convenience of these machines. Apart from its speed of process, HPF technology saves tube testing and cleaning, processes that are time-consuming and costly compared to conventional welding.
About Parker Hannifin
Parker Hannifin is a Fortune 250 global leader in motion and control technologies. For 100 years the company has engineered the success of its customers in a wide range of diversified industrial and aerospace markets. Learn more at www.parker.com or parker.southafrica@parkerhannifin.
Automation