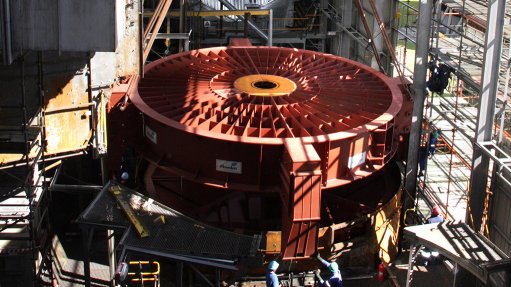
KEY SUPPORT BASE Howden supports its installed base of equipment through comprehensive maintenance contracts, spares supply and repair services
Boiler and cooling fan, airheater and gas cleaning equipment manufacturer and supplier Howden Africa will be participating in this year’s Power-Gen Africa (PGA) event to emphasise its aftermarket capabilities and customer support services for African utilities, including State-owned power utility Eskom, says company marketing and corporate affairs director Geoffrey Chingwaru.
He tells Engineering News that the company supports its installed base of equipment through comprehensive maintenance contracts and spares supply and repair services, as well as through equipment refurbishments and upgrades.
PGA will take place at the Cape Town Inter-national Convention Centre from July 15 to 17.
“Strong relationships between power utilities and their original-equipment manufacturer (OEM) systems suppliers are critical to ensur-ing long-term performance and adequate return on investment from coal-fired power stations,” says Chingwaru.
He adds that coal-fired power stations have plant service lifetimes of 30 years and beyond and, with extended service life, the issues of maintenance, refurbishment and upgrades require careful consideration and long-term planning.
“By their nature, coal-fired power stations experience high levels of abrasive wear and heat stress and are often subject to hard use in the winter months, which increases the need for maintenance and refurbishment. This support must come as cost effectively and efficiently as possible.”
In addition to scheduled maintenance pro- grammes, new technologies need to be incor-porated into existing plants – as they become available – to improve efficiencies, enhance performance and reduce costs, says Chingwaru.
He notes that power utilites such as Eskom cannot alone be expected to manage ongoing maintenance, refurbishments and improvements on the myriad systems under their control, which is why OEM aftermarket support is important.
“In a close, ongoing customer-supplier relationship, support can extend from the moment of commissioning to the end of the plant life, with the requisite maintenance spares and other backup provided on a contractual basis to optimise the process.”
Chingwaru tells Engineering News that Howden has followed this approach for coal-fired power stations in South Africa and that it has been able to provide critical aftermarket support, keeping many power stations operational.
He says offering 24/7 support to a coal-fired power station network such as South Africa’s requires significant investment in systems and personnel.
“Howden, for instance, has established a well-resourced operation in Middelburg, Mpumalanga, where we have equipment, spares and personnel to maintain our installed base of fans and airheaters,” says Chingwaru.
He says that, at PGA, Howden will ensure that it provides power utilities in Africa with evidence that the company is a world-class services and products supplier capable of engineering, designing, manufacturing and offering aftermarket support for boiler fans, airheaters, dry-cooling fans and gas-cleaning systems for the lifetime of coal-fired generating plants.