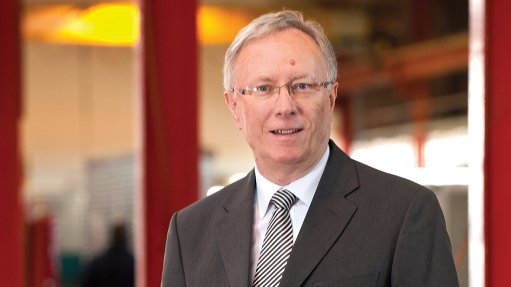
GERD SEUFFERT The SLAP system ensures reduced stock capturing time as the process becomes more automated with the use of barcode scanners
SEW-Eurodrive Johannesburg has released its new standardisation of logistics and assembly processes (SLAP) system, which has enhanced the company’s operational efficiency by about 40%.
“The system, which went live in March, was initially implemented at SEW-Eurodrive Germany. South Africa was the sixth country to implement the new system, which will be incorporated at its other branches over the next 24 months,” says SEW-Eurodrive general finance manager Gerd Seuffert.
SLAP is an information technology systems applications product (SAP) integrated system aligned with respective processes within the SEW factory facilities.
Further, the SLAP system ensures reduced stock capturing time as the process becomes more automated with the use of barcode scanners. This results in faster, measurable processes and better real-time information.
“Conservatively, it is safe to say we have seen a productive improvement of between 30% and 40%,” notes Seuffert.
He explains that the process of loading goods received from a container onto the system has been significantly reduced, as each container of goods has a barcode with information about the goods. A barcode scan captures all the items in the container without having to manually capture each item individually.
Seuffert adds that the SLAP system also significantly improved the automated tracking of goods, thereby improving customer information flow. He explains that, while dispatch matters had to be handled manually in the past, all dispatch items are now electronically logged, located and invoiced through the system, which can also automatically transfer data to a courier system through standardised message formatting.
Depending on the requirements, this triggers a carrier sticker or list, and allows for multiple deliveries through one transport or delivery group.
Seuffert indicates that the SLAP system has enabled factory workers, who have never had computer training, to become computer literate in a short period.
The system helps SEW-Eurodrive Johannesburg to better manage and control its stock. In addition to preventing loss of any items, it also allows for better planning and curtails the frequency of having to borrow parts for other jobs, which occurs when orders need to be filled in a hurry. Several confirmation points along the supply chain also enable users to pinpoint exactly where an item is.
“We are proud to have taken the first steps towards making this a reality in South Africa and look forward to bolstering our international ties through this initiative,” concludes Seuffert.