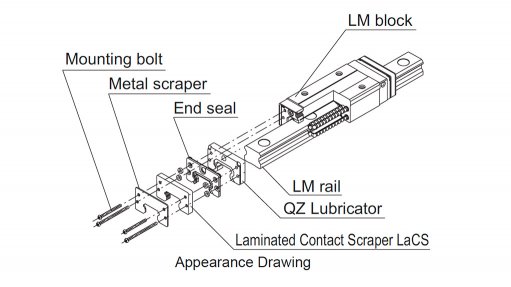
SEALING SOLUTION The LM block guide rail systems with the laminated contact scraper (laCS) system and sealing arrangement prevent potential seizures and failure
Motion-control solutions specialist DC Auto-Motion aims to increase local market awareness for the Japan-based THK linear-motion (LM) product range this year, emphasising the range’s suitability in welding and cutting machine applications.
DC Auto-Motion started representing THK in 2012 and was appointed as the official THK distributor for South Africa in mid-2014.
The THK range of LM systems, LM guides, ball splines, ball screws and electric actuators assists welding torch and cutting heads on the x-, y- and z-axes of machine applications to provide accurate and steady guidance.
“The THK LM systems are suited to the adverse environments of the welding and cutting industry, owing to the range’s LM block guides, which include the laminated contact scraper (laCS) system,” DC Auto-Motion director Dave Cawood tells Engineering News.
The system involves a laminated contact, three-layer scraper structure that removes minute foreign material, or liquid, which clings to the LM rail. Welding spatter or dust particles from cutting might also create this material and the laCS system prevents the material from entering the LM block, he explains.
Cawood adds that the system achieves low-friction resistance, as it uses oil-impregnated rubber with a self-lubricating function, called the QZ lubricator.
He further notes that the LM block guide rail systems with the sealing arrangement prevent potential seizures and damage, as well as premature machine failure. Another resulting benefit includes an extended block operation life.
Cawood adds that the laCS system enables the user to reduce costly downtime, citing international successes of the system, such as in the automotive and automation machine building industries, as well as steel cutting and welding machines.
The company presented the LM guide system with the sealing arrangement as a solution to a local glass manufacturer last year, and to a local sanitary ware manufacturer in early 2015.
LM Actuators
Cawood tells Engineering News that DC Auto-Motion will this year also focus on its THK KRF 5 LM actuator, which was launched in December 2014.
The THK KRF 5 fully enclosed, high-rigidity actuator series ranges from sizes 3 to 6. It employs an outer rail with a U-shaped cross section that enables it to accommodate a sizable moment load – a tilting load that attempts to rotate the rings of a rolling element bearing in a rotational manner perpendicular to the designed rotational axis. Moreover, the actuator body’s high rigidity allows for a compact, space-saving design.
Other features include strip seals on the side cover and upper surface that provide a fully enclosed structure. This prevents possible damage by foreign matter penetrating the unit from the surrounding environment. Additionally, the strip seals adhere magnetically, which reduces uplift and prevents gaps.
DC Auto-Motion supplied the THK KRF 5 actuator to a local plasma cutting machine manufacturer in early 2015 for use on the z-axis of the torch-height control system on one of the company’s assembled plasma cutting machines.
“DC Auto-Motion assessed the z-axis for the torch-height control, which is guided by . . . linear motion. “By introducing the THK KRF 5 actuator to guide the cutting head, the company provided an optimum solution that considerably reduced component costs and machining time,” Cawood says.
The KRF 5 was also introduced to a local alloy wheel inspection machine manufacturer to inspect accurate measurements on formula 1 forged magnesium wheels.
While Cawood believes that the laCS system and THK LM products are short-term premium, but long-term cost-effective options, he acknowledges the challenge of promoting the range locally for the company – manufacturers and end-users prefer to buy standard equipment for their welding and cutting applications based on price, and there is a lack of awareness about the benefits of LM products and the sealing arrangement.
“Nevertheless, there is significant potential in the South African manufacturing industry for THK products, including the automotive and beverage industries, where components are manufactured during high-volume processes,” Cawood concludes.