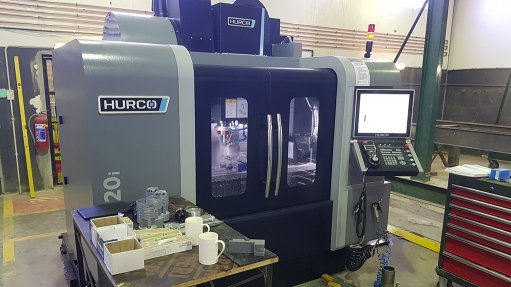
CoreSlab has taken further steps that have secured its position as a leading designer and manufacturer of pre-cast concrete items.
CoreEngineering, Coreslab’s state-of-the-art engineering arm, has commissioned equipment that will now allow the group to manufacture all the “cast-in” components for its comprehensive range pre-cast concrete items.
The engineering division has played an instrumental role in Coreslab’s ongoing success as a single source for all quality pre-cast concrete items. This division is tasked with manufacturing all componentry for the Spiroll Extenders and other capital equipment used in the company’s sophisticated batching plant.
“This in-house capability has provided us with the flexibility that is needed to ensure success in a very competitive market. Our customers will now be able to benefit from even greater levels of service from Coreslab. This includes faster response times and shorter lead times from the design phases through to delivery. Importantly, it will also ensure that we are able to do all of this while maintaining our high accuracy levels, a characteristic of our products that allows for their rapid installation on site,” Jaco de Bruin, managing director of Coreslab, says.
The Hurco VM20i computer-numerical controlled (CNC) machine was commissioned at CoreEngineering’s workshop this month.
The VM20i is a powerful CNC unit in the multinational original-equipment manufacturer’s range, and is equipped with the company’s fourth Axis and Winmax9 software. With a spindle speed of 10 000 revs-per minute, the VM20i is capable of accurately machining at 15,2 meters (m) per minute with rapids of 24 m.
De Bruin says that he opted for the VM20i because of Hurco’s reputable standing in the global steel-machining market that is in line with CoreSlab’s own exacting quality standards.
“Our decisions to purchase equipment for the engineering side or for the batching plant are not taken lightly. Extensive research was undertaken by our teams to ensure that we would purchase a machine that would also provide us with the high levels of accuracy that is needed to machine important componentry for the heart of the operation,” he says.
This follows a host of other developments at the company, including clinching a large contract for pre-cast items for a university residence expansion programme in Thoyandou and the supply of bespoke items for a hotel build in the area.