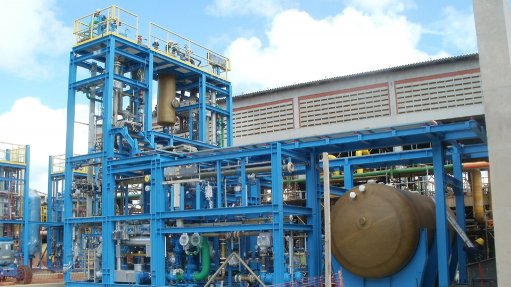
Thyssenkrupp Industrial Solutions’ modular skid mounted chlorine plants offer a cost-effective and practical solution to industries on the African continent who require small chlorine alkali plants for applications such as water treatment and mineral processing.
Bruce Bassett, Process Industries Senior Manager for Special Projects at thyssenkrupp Industrial Solutions South Africa, explains why their modular chlorine plants with a 15 and 45 ton capacity are particularly suited to the African market: “Many African countries import chlorine and caustic but the quantities are not large enough to sustain chlorine alkali plants.
Due to the vastness of the continent, getting these products up to African countries from South Africa for example, present tremendous logistical challenges which can increase the cost of the products four fold, simply making it economically unviable.”
While on-site chlorine production presents a better alternative to import, Bassett warns that setting up a chlorine plant presents its own challenges. Construction costs can sink a project and this is where our modular approach presents the simplest, fastest and most cost-effective solution for facilities that are remotely located and have limited engineering capabilities and staff resources.
Chlorine is produced through the process of electrolysis (the passing of an electric current through brine (sodium chloride (NaCI) or common salt dissolved in water), with salt as the feedstock. Two co-products that result from chlorine production are caustic soda (sodium hydroxide, NaOH) which is an alkali and hydrogen (H2) which is a combustible gas.
In the modular solution, electrolysis is built on multiple skids that fit into 40 foot containers that can be easily, quickly and cost-effectively transported to site.
Construction and assembly is also fast and easy, needing only a small team, leaving only the non-modular plant sections to be stick built. Rapid project implementation and plant start up time result in substantial savings in terms of construction time and costs.
“Our modular engineered solutions have innovated processes through simplification,” comments Bassett. Designed and manufactured by thyssenkrupp Uhde Chlorine Engineers of Milan, Italy, skid mounted chlorine plants are made of a different functional skid groups such as brine filtration, brine super purification, and sodium hypo production. In addition to new plants, these group modules can be installed in existing facilities for modernisation and debottlenecking.
Pre-testing, quality control and quality checks are done at the workshop in Europe during pre-assembly of the skid units, mitigating construction risks and reducing testing activities in the field. Mechanical connections, electrical wiring and, where possible, pressure tests are all performed in the workshop. Tolerance testing in the workshop also guarantees trouble free field installation.
thyssenkrupp combines global technology with local knowledge to offer a complete turnkey EPC solution – from feasibility studies and plant design including geotechnical information and civil works, through to all necessary infrastructure, construction commissioning and O&M. “Plants also need power and here too we can assist. Instead of being vented into the atmosphere, we capture the excess hydrogen in fuel cells, a co-product resulting from chlorine production, to produce energy. This method can generate up to 0.8 megawatt of power.”
“Once a plant is operational, we continue the partnership with our customer through our full service offering that includes ongoing training and after-sales support,” concludes Bassett.
Today there are skid mounted chlorine plants in operation in Europe and South America, and Bassett confirms that they are currently working on a feasibility study for the development of a plant in South Africa.