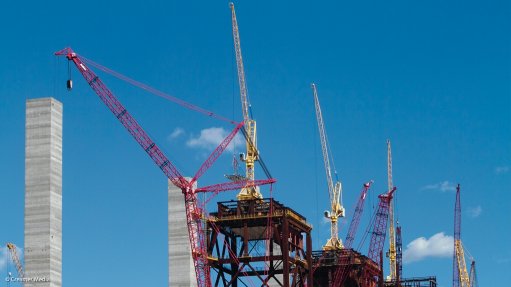
MEDUPI POWER STATION
The FGD will allow Medupi to comply with the new plant cabon dioxide minimum emission standard
Photo by: Duane
State-owned power utility Eskom intends to retrofit each of the Medupi power stations’ six power generation units with flue gas desulphurisation (FGD) technology, which is used to reduce the sulphur dioxide (SO2) emissions of a coal-fired power station but has the drawback of requiring high water consumption.
Independent environmental engineering consultant Jane Reddick notes that, once FGD is fully installed, it will enable Medupi to comply with the new plant SO2 Minimum Emission Standards under the South African National Environmental Management: Air Quality Act (NEM: AQA), which stipulates that, for coal-fired power stations, daily average SO2 emissions should not exceed 500 mg/Nm3.
Further, Reddick points out that the project is currently in the environmental- authorisation application phase, where the environmental-impact assessment (EIA) is being conducted as part of the process. She also points out that it is expected that the first FGD unit will be retrofitted in 2021.
Moreover, she highlights that, with a variety of technologies available to reduce SO₂, Eskom chose to fit Medupi with the wet limestone open spray tower FGD, which is the most water-intensive technology, instead of the more water-efficient circulating dry scrubber (CDS) process.
She explains that, in the wet FGD process, limestone is mixed with water and sprayed onto the flue gas inside the absorbers so that the SO2 reacts with the limestone and oxygen to form crystalline gypsum, which reduces the SO2 concentration of the flue gas by more than 90%, adding that the gypsum can then be dewatered and sold to various markets, such as the construction industry.
FGD Challenges
Reddick says Eskom’s choice to install wet limestone FGD at Medupi raises a few concerns because of the project’s increased water consumption.
She explains that the total yearly water requirements for the plant are about 15.4-billion litres – about 9.4-billion litres for the wet FGD process and another six-billion litres for the power station. The wet FGD process also produces wastewater that will have to be treated, and the resulting chemical sludges disposed of, she adds.
Medupi is located in the water-scarce Lephalale municipality, in Limpopo, and will require more water than is currently available in the catchment area once all six FGD units are operational, Reddick states.
She points out that the Mokolo and Crocodile West Water Augmentation Project is, therefore, being developed to supply additional water to the region, including Medupi.
“However, the water augmentation project is already several years behind schedule and, even if it is completed in time for the Medupi FGD project, periods of water shortages are anticipated, with scenarios suggesting regional shortages of up to 16-billion litres a year . . . over a period of up to 19 years.”
Because Eskom is classified as the only ‘strategic water user’ in the National Water Resource Strategy, the Department of Water and Sanitation supplies water to the utility at a 99.5% assurance level, which implies that the risk of failure to supply water is once in 200 years. Reddick notes that the expected regional water shortages are, therefore, likely to disproportionately affect communities, farmers and other nonstrategic water users within the catchment.
FGD Solutions
However, she says a design modification has been identified that could potentially reduce the FGD water consumption by about 30% to levels comparable to those of CDS technology.
It involves installing an inlet flue gas cooler, which essentially reduces the temperature of the flue gas before it enters the FGD system, thereby reducing the amount of water that is evaporated in the FGD absorber and, hence, is lost through the exiting flue gas.
“Unfortunately, the cooler has not yet been included in the FGD project design. It is not expected to add to the project’s life-cycle costs, but even if further analysis identifies that it will increase costs, it plays a critical role in addressing the project’s water-related impacts . . . and, therefore, should be incorporated into the FGD design or, at the very minimum, be considered as a design alternative for assessment and public participation in the EIA process,” she states.