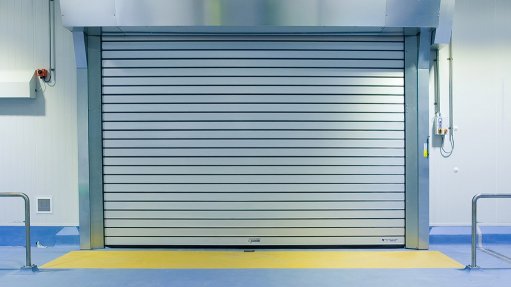
The Albany high performance door supplied and installed by door and loading dock specialist, Maxiflex, has improved uptime and production at a leading Eastern Cape automotive manufacturer’s laser facility.
The original door system at the automotive company’s class 4 laser cabin was proving to be slow and costly. Frequent downtime ensuing from long service periods, regular breakdowns and complicated maintenance was compounded by the fact that the door caused damage to its own structure and apron.
“The laser cabin demands a high quality, ultra-reliable door that is specifically designed and engineered to meet all the specifications required by this highly specialised application to ensure the safety of personnel and prevent damage to equipment,” explains Maxiflex Regional Service Coordinator, Theo Du Preez.
“With high speed and very little or no downtime prerequisites for the customer, a more reliable, efficient and cost-effective door system for the laser cabin was urgently needed. When Maxiflex was given the opportunity to present a solution, we did not hesitate in recommending the Albany RR3000 high performance laser protection door complete with a Motor Control Centre (MCC).”
Part of the renowned ASSA ABLOY Entrance Systems’ stable of quality automated entrance solutions, the Albany RR3000 presented the perfect fit. In addition to the fact that the door shares similar specifications with the other laser doors in the cabin, Albany represents everything the customer requires from a protection door system – superior quality, reliable high speed performance, long lifecycle, low maintenance, and fast repair.
The Albany RR3000 qualifies as a laser protection door thanks to its double-walled panels and the special design of its profile overlaps that create a labyrinth of two profiles. As a result of this unique construction the labyrinth connections between the panels prevent the laser beam from burning through the aluminium door curtain.
During EN 60825-4 compliancy tests conducted with a 4,6 kW laser at a focus distance 2, the laser beam did not burn through the curtain after 60 seconds. The door conforms to EN ISO 12100 and EN 1088 and the safety switches are EN ISO 13849-1 and EN 62061 accredited.
The Albany door’s reliable (Bonfiglioli) power unit is complemented with an intellectual MCC vector control to assist with the interphase between the door and the Programmable Logic Controller (PLC). The Albany RR3000 uses two sets of photocells to prevent a crash in the door line. Two safety switches fitted on each side informs the PLC that the door is closed and that the cabin is safe for laser procedure to commence. The switches will also inform the PLC if the door is obstructed by a part or is running skew.
The low friction door is controlled by potential-free contacts and rapid opening and closing ensures a short cycle time. Du Preez adds that the door speed can be increased through a simple software upgrade.
In the event of a crash, instead of having to remove the complete door leaf for repair or replacement which causes excessive downtime, unlike most doors, it’s possible with the Albany system to remove or replace only partially damaged lamellas. This ensures a short downtime period and consequently minimal loss to production. Downtime is further reduced with the Albany door’s virtually service-free drive system and quick mechanical repair.
Installation presented a number of challenges; unlike the previous door which was installed on the outside of the door opening the Albany door had to be installed on the inside of the door opening and the installation was a left- and right-hand part bed inside the cabin that could not be moved under any circumstances.
“But our smart engineering team found a solution and despite a number of essential modifications, we completed the installation way ahead of schedule at the end of 2016,” affirms Du Preez. Commissioning took place in January 2017 and Maxiflex provided technical training.
The customer expressed complete satisfaction with the performance of the Albany door which had completed 80 500 cycles over a four month period with no reported breakdowns. “100% uptime has increased the speed of the parts coming out of the cabin,” adds Du Preez who confirms that the customer has already purchased another MCC with upgrade software to increase the door speed even further.
Maxiflex is currently responsible for servicing the RR3000 Albany door as part of a service contract agreement with the customer.
The Albany door protects personnel against flying (welding) sparks, dust and noise (protection up to 25dB(A)) and the system is ideally suited as a machine protection door for a wide range of laser applications including automatic welding, cutting and painting systems as well as milling machines, and workpiece handling.